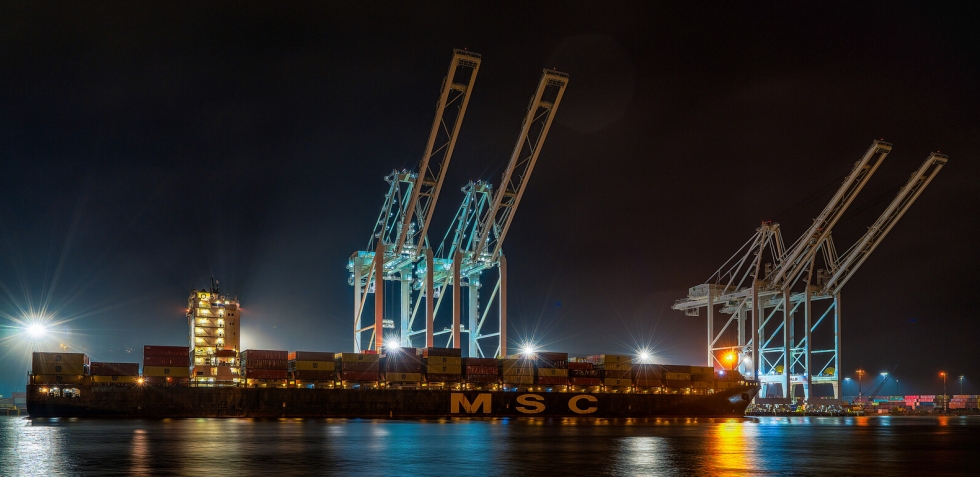
SSA Marine and The Northwest Seaport Alliance Welcome First Vessel Call to Modernized Terminal 5 in Seattle
Jan. 10, 2022 - Phase one of Terminal 5 is open for cargo ships to call the NWSA gateway. The MSC Monterey is the first vessel to call the newly modernized terminal with four new Super-post Panamax cranes ready to work the ship. The Terminal 5 Modernization Program launched in 2016 to expand gateway cargo capacity and enable The Northwest Seaport Alliance to service the largest vessels in the Transpacific trade.
“The opening of Terminal 5 will add an additional berth to our gateway at a time when the supply chain is under increased pressure. We are the only gateway bringing additional berth capacity to our harbors on the West Coast at this critical time. By adding additional deep-water terminal space, we can serve the largest vessels in the industry and increase cargo volumes that benefit our local, state, and regional economy for years to come,” said Port of Tacoma Commission President and NWSA Co-Chair Don Meyer.
“The modernization of Terminal 5 was a strategic decision made by Managing Members at the establishment of The Northwest Seaport Alliance. The opening of phase one of Terminal 5 is a significant milestone for our gateway. This investment will increase our ports’ competitiveness, support additional maritime jobs, and reduce our environmental impact by enabling ships to use shore power rather than running their generators while at berth,” stated Port of Seattle Commission President and NWSA Co-Chair, Ryan Calkins.
“We are proud to have invested along-side and work with the Northwest Seaport Alliance to bring on this much needed additional T5 terminal capacity. Larger ships and increased volumes are coming and we want to be ahead of the curve in meeting our customer’s needs” stated Ed DeNike, President of SSA Terminals.
“The opening of Terminal 5 adds another berth to the Seattle harbor and supports more jobs, local businesses, and economic growth across our region. The men and women of the ILWU continue to be ready to move more cargo through The Northwest Seaport Alliance gateway”, stated Rich Austin President of ILWU Local 19.
Construction on the new facility launched in July 2019, fueled by the combined investment from the NWSA Managing Members and SSA Marine of approximately half a billion dollars. The strategic investment of modernizing Terminal 5 will increase cargo capacity and job opportunities in the Puget Sound region. The terminal renovations include two reconfigured berths to support larger cranes, on-dock rail, 1,500 refrigerated plug-ins, and shore power capability.
Terminal 5 is equipped to support both efficiency of operations and the surrounding environment. On-dock rail will play a significant role in helping to reduce truck traffic around the Terminal with discretionary cargo headed for the mid-west being loaded directly onto railcars instead of loading on trucks to move off-terminal. The terminal’s shore power capability will reduce vessel emissions while at berth. Vessels will be able to plug into the electrical grid and utilize cleaner energy than burning fuel. This will reduce negative impacts to surrounding near-port communities and help the NWSA reach its emission reduction targets.
SSA Terminals purchased four Super-post Panamax cranes which were delivered to Terminal 5 and commissioned for use in 2021. Each crane stands 316 feet tall with a 240-foot outreach boom and can lift 65 tons providing increased capacity and job opportunities for our region. Labor began working the first vessel on January 7th.
Phase Two of the Modernization program is underway with operations in the south berth expected to be complete in mid-2023. At full completion, Terminal 5 will boast 185-acres of additional capacity. Beyond import cargo, the opening of Terminal 5 will also help increase opportunities for agriculture exporters from the mid-west and eastern Washington to move their goods to overseas markets.
SOURCE: The Northwest Seaport Alliance |
|
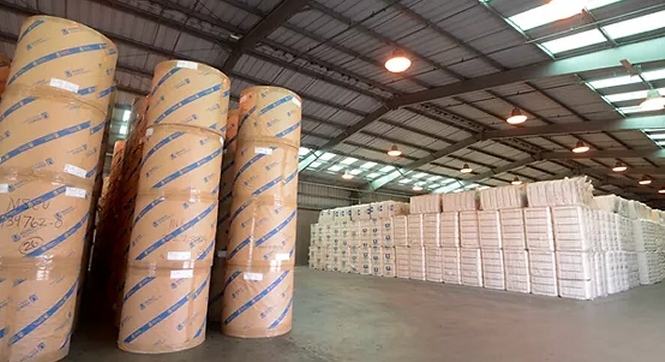
Precision Terminal Logistics Acquires The Kearney Companies
Jan. 17, 2022 - Precision Terminal Logistics (PTL), effective December 31, 2021, acquired The Kearney Companies, Inc. (KCO) of New Orleans, Louisiana and Kearney Page Warehouse Services (KPWS) operating in Savannah, Georgia.
KPWS will be rebranded as The Kearney Companies – Savannah. David Kearney will retain his position as president of both companies and will continue to be an equity owner.
PTL President Ray Nixon said, “The acquisition expands two critical gateways at a crucial time when customer supply chains at ports are backlogged and need enhanced capacity.”
PTL’s owners, Anacostia Rail Holdings (ARH) and Brown Brothers Harriman Capital Partners (BBH), will provide additional resources and strategic partnerships to the companies and their clients.
Today, KCO operates more than 500,000 square feet of rail-served warehouse capacity and 60 acres of yard capacity in the Port of New Orleans gateway. These facilities are served by the New Orleans Public Belt Railroad (NOPB) that connects directly with six U.S. Class I railroads (BNSF, CN, CSX, KCS, NS, UP).
KCO’s services include commodity warehousing, barge and rail transloading, coupled with full-service ocean container drayage operations and inland freight management services. KCO handles agriculture and manufactured products including corn meal, rice, paper, chemicals, lumber, steel and non-ferrous metals products.
The Kearney Companies – Savannah operates a 400,000 square foot warehouse in Garden City, Ga. near the Georgia Port Authority - Savannah Container Terminal, served by CSX. Kearney manages high volume cross-dock programs for numerous commodity suppliers especially in the pulp and paper sector, supported by an advanced logistics technology platform.
Nixon notes, “Combining Kearney’s expertise in warehousing with PTL’s experience in material handling expands the service products that PTL can provide to shippers. Our geographic expansion offers clients additional resources and creative logistic solutions.”
David Kearney, president of KCO said, “The initial investment by PTL in KCO and KPWS, coupled with PTL’s access to capital, ensures that we are poised for immediate expansion in our existing markets driven by our customers’ need for more capacity. Further, with the support of PTL, we can target new, strategic markets where our customers have supply chain needs. We could not be more excited about the doors this will open for us. Additionally, PTL brings operational expertise to ensure we continue to strive for the highest standards in workplace safety, supply chain technology, and environmental responsibility.”
Precision Terminal Logistics Services
Precision Terminal Logistics, headquartered in the Pittsburgh, Pennsylvania area, operates 23 terminals in 15 states. PTL provides an array of material handling services including transloading, secure bulk commodity storage and material handling facility design. |
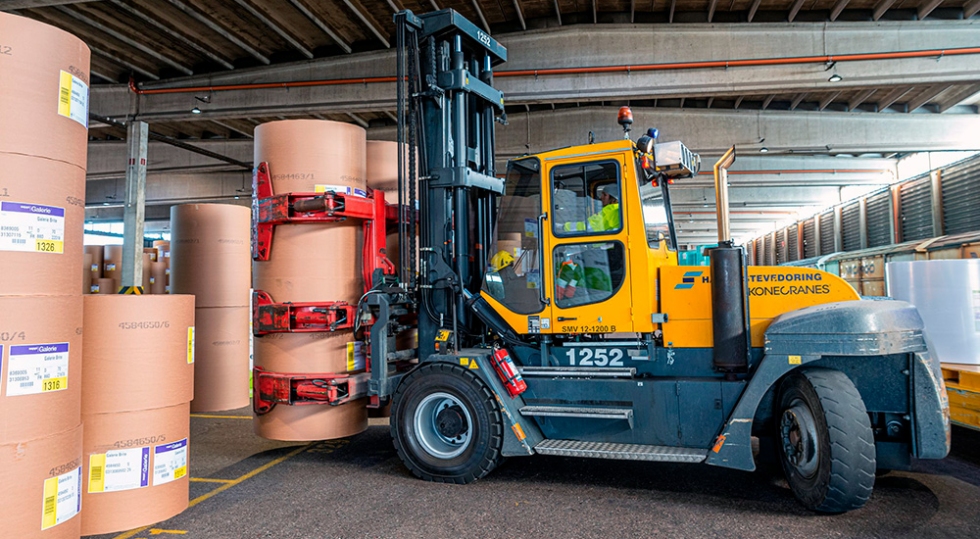
Metsä Board Sells Hangö Stevedoring in Finland to Euroports
Dec. 21, 2021 - Metsä Board and Euroports have signed an agreement on 16 December 2021, according to which Metsä Board will sell the entire share capital of its fully owned subsidiary Oy Hangö Stevedoring Ab to Euroports Finland Oy.
Hangö Stevedoring is a port operator in the Port of Hanko and its business is not part of Metsä Board's core business.
The parties have mutually agreed that the transaction price will not be disclosed.
Hangö Stevedoring has around 180 employees and its sales in 2020 were approximately EUR 20 million. The company is the largest provider of cargo handling services in Hanko and has a wide customer base, including Metsä Board.
“We are very excited to join Euroports,” says Petteri Sammalisto, Managing Director of Oy Hangö Stevedoring Ab. “We are looking forward to identify several shared opportunities between the companies and look forward to bringing the enhanced service offering to our customers.”
Euroports Finland is a leading port operator in Finland. The company is part of Euroports Group, one of the largest port-infrastructure companies in Europe, with around 3,000 employees worldwide and approximately 600 in Finland.
The transaction is expected to be completed in the first quarter of 2022.
SPOURCE: Metsä Board and Hangö Stevedoring |
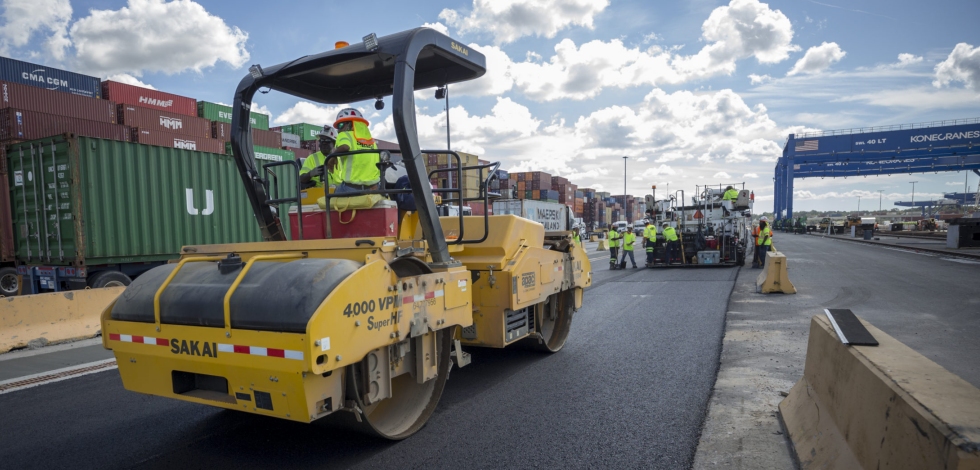
Georgia Ports Authority Capacity Efforts Paying Off
Savannah marks 16 consecutive months of record growth.
Dec. 10, 2021 - The Port of Savannah handled 495,750 twenty-foot equivalent container units in November, a 6.7 percent increase over the previous year and a new monthly record for the Georgia Ports Authority.
“I would like to acknowledge the incredible teamwork on and off our terminals that have made these results possible,” said Griff Lynch, GPA’s executive director. “Our employees along with Savannah’s stevedores, ILA members, truckers, river captains and many other transportation professionals have pulled together to handle record cargo volumes for an incredible 16 consecutive months. Off terminal, the willingness of our customers, two class one railroads and stakeholders in state and federal government, have allowed us to put into place innovative and effective supply chain solutions.”
In less than six months, the GPA has designed and begun to bring online an ambitious series of improvements that will increase the Port of Savannah’s annual capacity by 25 percent. Already, 200,000 TEUs of container handling space have come online, with an additional 200,000 to be added in just three weeks. By March 2022, an additional 500,000 TEUs will be added, growing to a total of 1.6 million of new capacity by June.
GPA is also expediting the completion of its Berth 1 expansion which will add 1 million TEUs of new berth capacity and eight ship-to-shore cranes at its docks. The project is now 30 percent complete and will come online at the end of Q2, 2023.
“Through the cooperation of our customers and the innovative thinking of our operations team, we’ve trimmed the number of boxes on terminal to allow for more efficient container handling and faster vessel service,” said GPA Board Chairman Joel Wooten. “Additionally, crews are working every day to build the new container yard and dock space that will keep commerce flowing.”
Off-terminal, GPA has activated four flexible “pop-up” container yards near manufacturing and distribution centers. The sites in Atlanta, Savannah, Statesboro, and Murray County in Northwest Georgia bring cargo closer to customers and reduce the length of container storage time at the Port of Savannah. The GPA is also arranging additional sites, which will bring the total annual capacity for the off-port locations to 500,000 TEUs.
SOURCE: Georgia Ports Authority |
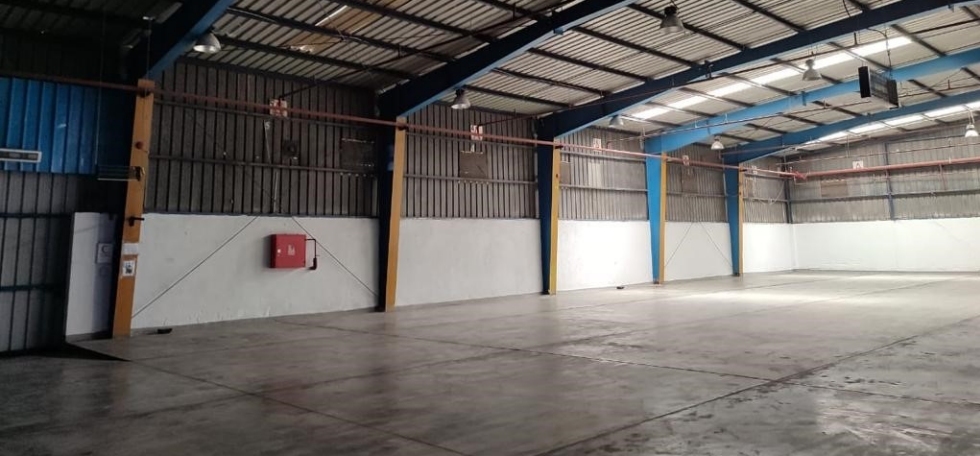
Alexander Global Logistics Now Offers QAKE Certified Pulp and Paper Warehouse in Alexandria Port
Nov. 11, 2021 - Alexander Global Logistics (AGL) announced that it recently acquired a warehouse facility in Alexandria, Egypt, for the handling of pulp and paper shipments.
According to AGL, the acquisition was prompted by a North American pulp and paper producer seeking a fully equipped, bonded warehouse dedicated to pulp and paper that also needed to be QAKE (Quality Assurance Key Environment) certified within a six-month timeframe. This meant special hygiene and maintenance measures, qualified and trained personnel, modern technology, GMP specifications, and more.
In addition, COVID-19 protocols were in-place and tasks such as on-site inspections were not always possible.
“With our international team of highly qualified staff members as well as our partner company located directly in Alexandria, we were able to conduct our regular inspections and training remotely,” AGL said. “The well-being of all involved are of utmost priority, therefore we reacted quickly in making sure all health standards were met to prevent the spread of the pandemic and to keep everyone safe.”
Renovations of the warehouse started with a new roof, flooring, lighting, and paint. Installations of EDI to track the inventory efficiently, modern pest control devices and disinfectant stations, were also carried out as part of the conditions prior to the audit taking place. AGL provided training videos shown from previous AGL projects to all personnel, as well as weekly video calls to ensure everything was communicated clearly and that all requirements were being met.
The upgraded warehouse in Alexandria Port includes modern handling equipment (e.g. electric forklifts) with a storage area of 2.000 m² and an outdoor storage yard of 20.000 m². Along with humidity and temperature control system, the facility now provides the foremost services for AGL’s client and becomes one of many dedicated warehouses worldwide suitable for pulp and paper that AGL offers.
AGL noted that the project was completed on-time and on-budget, and has successfully become the fourth warehouse worldwide to be QAKE certified.
“Through our in-house developed AGL-Web, we can offer our customers a tailor-made solution that fits their needs. AGL-Web enables customers to monitor stock levels in real-time and have them integrated into their IT System. Additionally, pulp producers can use AGL web to control inventory and provide Vendor Managed Inventory (VMI) solutions to their customers,” the company added.
SOURCE: Alexander Global Logistics |
|
|