|
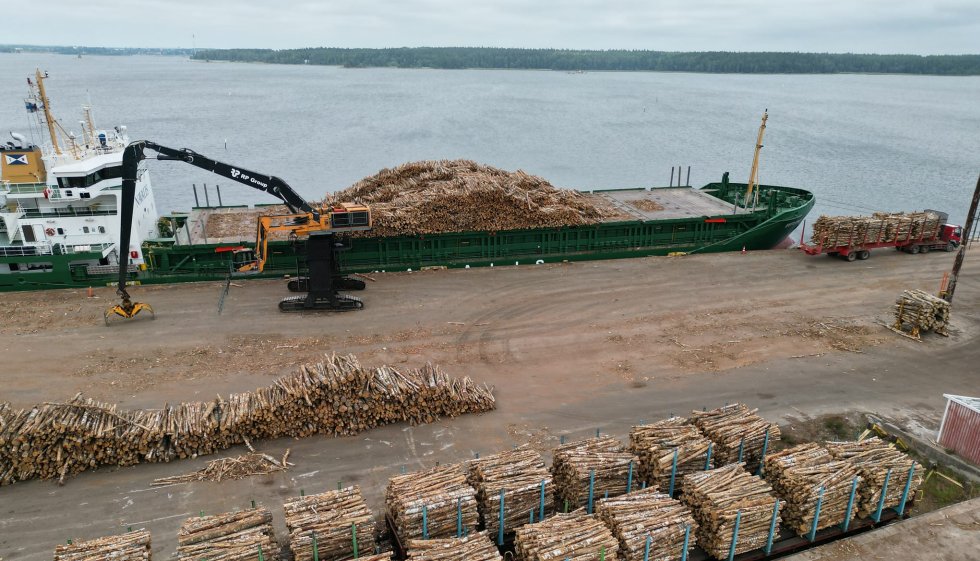
Euroports Finland Buys Substantial Part of BB Logistics Oy
Dec. 30, 2022 - Euroports Finland Oy and the owners of BB Logistics Oy have signed an agreement, according to which the owners of BB Logistics will sell a substantial part of the company to Euroports Finland. The agreement brings together two innovative companies that share a commitment to providing the highest quality maritime supply-chain solutions to customers across the globe.
BB Logistics is a fast-growing, reliable logistics service provider operating in five ports in Finland: Kemi, Oulu, Kristiinankaupunki, Kaskinen and Hamina. The company has 40 employees, who will continue to work for BB Logistics. The name of the company and the current management team will remain unchanged.
Euroports Finland is the leading full-service port operator in Finland. The company provides a range of port services, including value-added services, with the highest standards of safety and quality, focusing on the sustainability of its operations. Euroports Finland is part of the international Euroports Group, which operates in approximately 50 terminals and logistic platforms globally and has a workforce of more than 3,000 employees.
“As part of Euroports Group Strategy supported by our Shareholders (RLogitech, FPIM, PMV) we are very pleased to be able to develop further our footprint in Finland with the investment into BB Logistics port operator in five terminals in Finland,” said Frédéric Platini, CEO Euroports Group. “This acquisition will complement our position both from a geographic as well as a commodity perspective in the Baltic Sea area with our existing terminals in Rostock, Rauma, Hanko, and Pietarsaari.”
Kim Lindström, Managing Director of BB Logistics, added, “We are excited about the new partnership with Euroports. We share the same logistic DNA which allows us to support our customers to be successful worldwide. Providing efficient logistics services is at the core of our service package.”
SOURCE: Euroports |
|
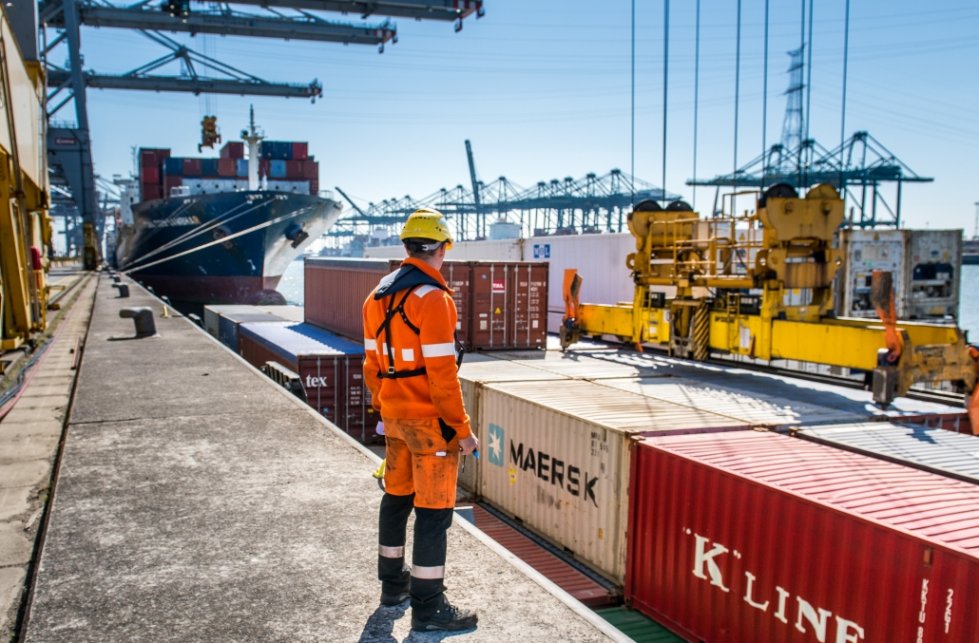
Port of Antwerp-Bruges Provides Update on Certified Pick up
Dec. 28, 2022 (Press Release) - The terminals on the Antwerp port platform are further preparing themselves to implement Certified Pick up, the container delivery process based on identity rather than PIN codes. In the context of a digitally secure port, the implementation of Certified Pick up is one of Port of Antwerp-Bruges' priorities. Over the past few months, a lot of optimisations have taken place, in order to tailor the process even better to users' needs.
A clear customs light
Certified Pick up brings users more transparency about the delivery process of a container. Customs status is an important factor in this. In recent months, we have been working hard with the port community, customs, NxtPort and Port of Antwerp-Bruges to improve and extend the quality of the customs light of a container (CCRM). We have thoroughly tested the forwarding of the customs light messages and solved technical hick-ups together with customs step by step.
Furthermore, additional reporting and the development of port equalisation provides more transparency and makes the process operationally more efficient. Thus, the customs status of a container can be proactively monitored by multiple parties including shipping companies, forwarders and transport operators.
The new transparent customs light will be available during the first quarter of 2023. After a transition phase, the light will eventually become mandatory to be able to take containers away from the terminal.
Uniform procedures
Different partners in the supply chain handle the import process of a container differently. To achieve an optimal digital process, standardisation is needed. We mapped these different import processes and their settlement and established a uniform way of working. This was necessary to digitise the process and make it more efficient. These processes will soon be available as manuals and best practices.
Who is on board?
Certified Pick up is currently in operation at PSA's terminals (Q 869 and 913). DP World Antwerp Gateway and MPET will follow shortly. In addition, just about all shipping companies are connected and we are taking the final steps to make the release for truck operators go smoothly. We developed extra functionalities in the user interface to adjust larger volumes in one go. In the next phase, we will also implement this for inland shipping and rail.
In total, about 2,000 companies are registered on Certified Pick up today.
In order for the rollout to continue smoothly, we call on all parties to actively start using Certified Pick up already, receive the release right and then forward, accept, reject or revoke it. Only in this way can we ensure a smooth elimination of PINs soon.
A multidisciplinary team from Port of Antwerp-Bruges and NxtPort is working full steam ahead to ensure a further successful roll-out in 2023.
You can always contact the project team for questions at [email protected]. General information on this project can be found at www.portofantwerpbruges.com/cpu.
SOURCE: Port of Antwerp-Bruges |
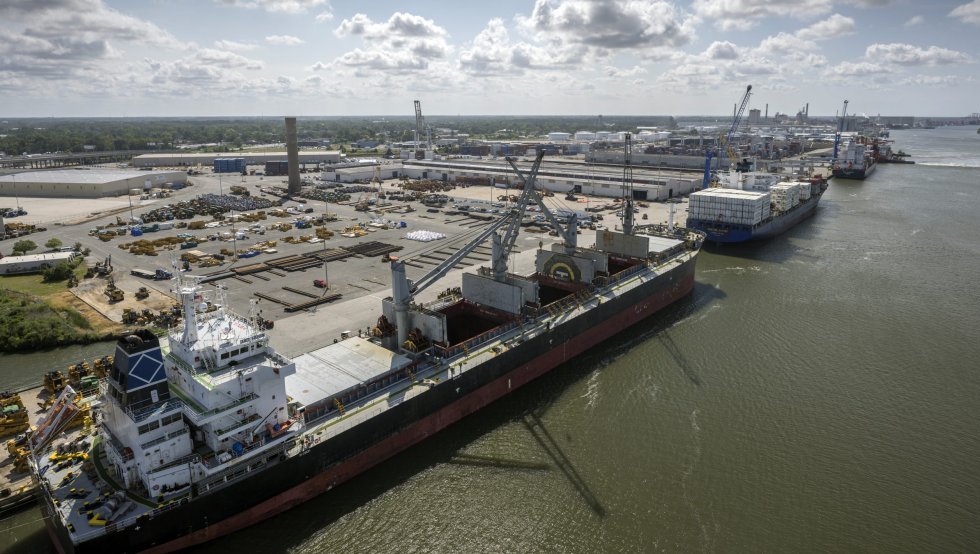
Georgia Ports Authority to Renovate Ocean Terminal Docks at Savannah
Dec. 12, 2022 - The Georgia Ports Authority Board has approved a plan to renovate and realign the docks at the Port of Savannah’s Ocean Terminal to better accommodate its expanding container operation.
“For nearly 40 years, Ocean Terminal has been handling a mix of container ships and breakbulk vessels. The realignment is part of a broader effort to transform the terminal into an all-container operation, shifting most breakbulk cargo to the Port of Brunswick,” said Griff Lynch, GPA executive director. “Completion of this project will improve our flexibility and allow Georgia Ports to optimize cargo movement, supporting our customers in delivering goods to market efficiently.”
GPA plans to shift breakbulk cargo carried by Wallenius Wilhelmsen Ocean to Colonel’s Island Terminal in Brunswick. Construction has started on 360,000 square feet of dockside warehousing that will serve auto processing, as well as three additional buildings and 85 acres of auto storage space on the south side of the island.
Ocean Terminal
The 200-acre Ocean Terminal facility will be modified in two phases.
Work will begin with rebuilding the docks to provide 2,800 linear feet of berth space, capable of serving two big ships simultaneously. The docks will be served by new ship-to-shore cranes. On Tuesday, the GPA Board expanded its crane purchase by one, for a total of eight cranes slated for Ocean Terminal.
“As the dock construction progresses, GPA will continue to operate container ships at Ocean Terminal,” said Ed McCarthy, chief operating officer at Georgia Ports. “The work – which is funded by GPA’s Series 2022 Revenue Bonds – will be conducted alongside container and breakbulk operations."
Apart from new cranes and berth enhancements, the overall project will bring expanded gate facilities and paving to allow for 1.5 million twenty-foot equivalent container units of annual capacity. Wharf renovations are slated to start in January 2023, with completion of the entire terminal redevelopment expected in 2026.
The Port of Savannah is coming off its busiest October ever, in which it handled nearly 553,000 TEUs. Port officials expect container volumes to taper downward toward the end of the year. Lynch said the opening of a new container berth at Garden City Terminal next summer and volume declining from historic highs will help expedite vessel service, which saw backlogs during the height of demand.
“While we are beginning to see an anticipated market correction, it is important that GPA move forward with projects like the Ocean Terminal enhancements to accommodate business growth,” said GPA Board Chairman Joel Wooten. “Through continued infrastructure improvement, we will ensure the free flow of commerce, and our ability to meet expanding customer demand.”
Over the past year, the GPA Board has approved $1.17 billion in infrastructure advancements, including expansions to berth, container yard and rail infrastructure. |
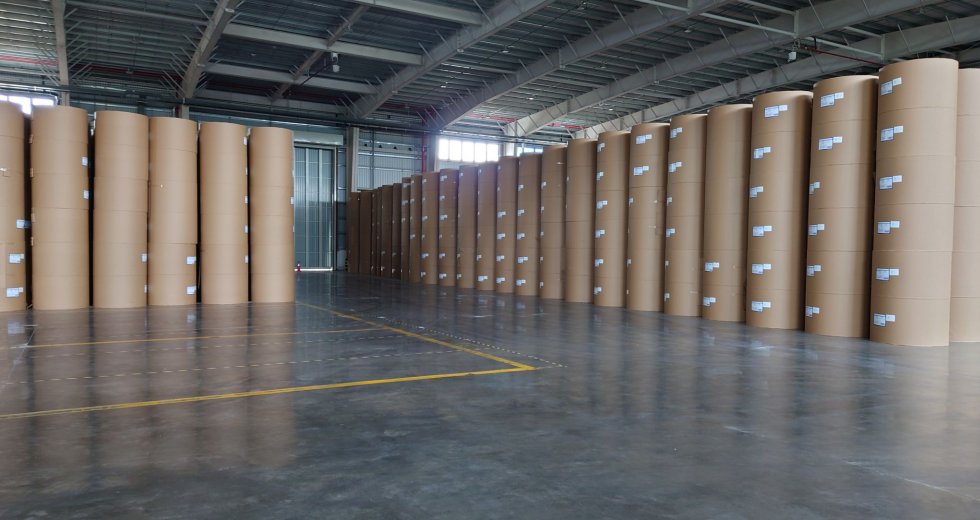
Euroports Inaugurates Three New Berths for Forest Products at Its Gaolan Terminal in South China
Nov. 22, 2022 - Euroports is pleased to announce the inauguration of three new berths at its Gaolan Terminal in South China. Furthermore, the company expects another berth to be approved for international cargo by the end of 2022.
The new area grants Euroports a total of five berths for forest products operations.
Earlier this year Euroports built a new warehouse in Gaolan designed to optimize breakbulk in – container out operations, allowing the port operator to better serve destinations for containerized cargo in China and Southeast Asia.
“These developments, along with continued investments in infrastructure, equipment, and labour resources, reinforce Euroports’ strategy to offer our customers a first-class terminal for the operation of forest products in the region,” the company said in a press release.
“A special thanks to our partners ZPH and ZICT for their unwavering dedication to the development of Gaolan Terminal,” Euroports added.
SOURCE: Euroports |
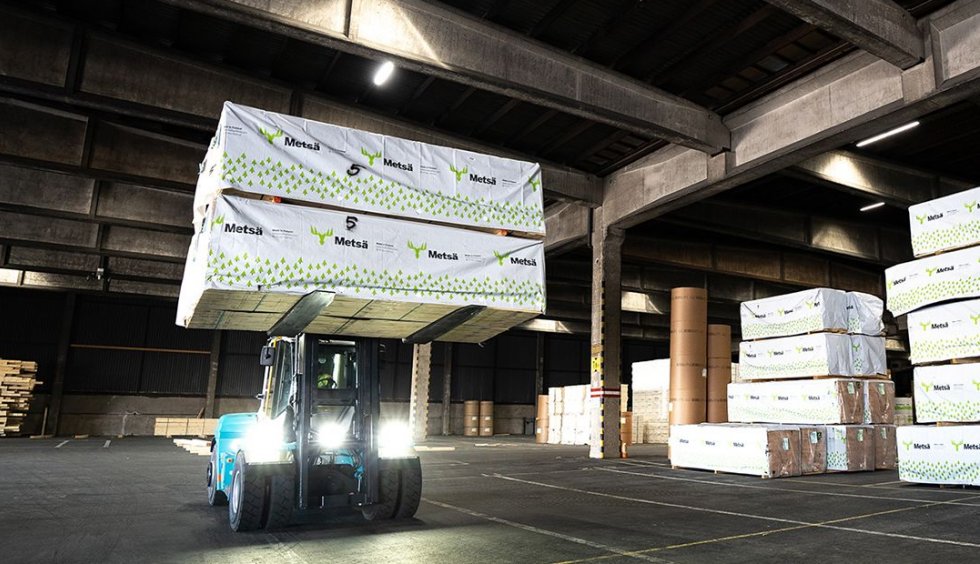
Euroports Rauma Oy Handles Terminal Operations for Metsä Fibre’s New Sawmill
Oct. 20, 2022 - Metsä Fibre on Sept. 30 started production at its new sawmill in Rauma, Finland. The new sawmill has an annual capacity of 750,000 cubic metres of pine sawn timber, and the annual use of pine logs sourced in Finland is around 1.5 million cubic metres. The sawn timber produced in Rauma is sold mainly to Europe and Asia.
The sawmill’s location enables smooth logistics to transport the sawn timber to customers through the Port of Rauma. The new sawmill does not have its own warehouses. Instead, finished sawn timber is packaged and automatically loaded onto lorries, which transport it directly to the port.
Euroports Rauma Oy is responsible for the sawmill’s terminal operations. The total annual volume of the Rauma sawmill will nearly double the timber volume processed by Euroports Rauma, making the company the second largest timber operator in Finland.
“The close corporate cooperation behind the Rauma sawmill helps ensure that the wood value chain is environmentally friendly and cost-efficient,” says Sari De Meulder, Managing Director of Euroports Finland Oy.
Euroports Rauma has recently invested in the processing of timber.
Tuomas Saarnilahti, Business Unit Manager of Euroports Rauma, explains, “We use modern containerisation equipment, as well as forklifts designed for timber processing. We have also purchased a new hybrid crane that can be operated entirely on electricity. In combustion engines, we use biodiesel as fuel.”
Euroports Finland Oy’s companies are committed to mitigating negative environmental effects and establishing a safe and healthy working environment.
“Safe movement and passage were key factors in the design of the timber terminal, and we are investing in the constant reduction of carbon dioxide emissions produced by fossil fuels and the minimisation of environmental effects caused by our operations,” concludes Tuomas.
SOURCE: Euroports and Metsä Fibre |
|
|
|
<< first < Prev 1 2 3 4 5 6 7 8 9 10 Next > last >>
|
Page 8 of 31 |