|
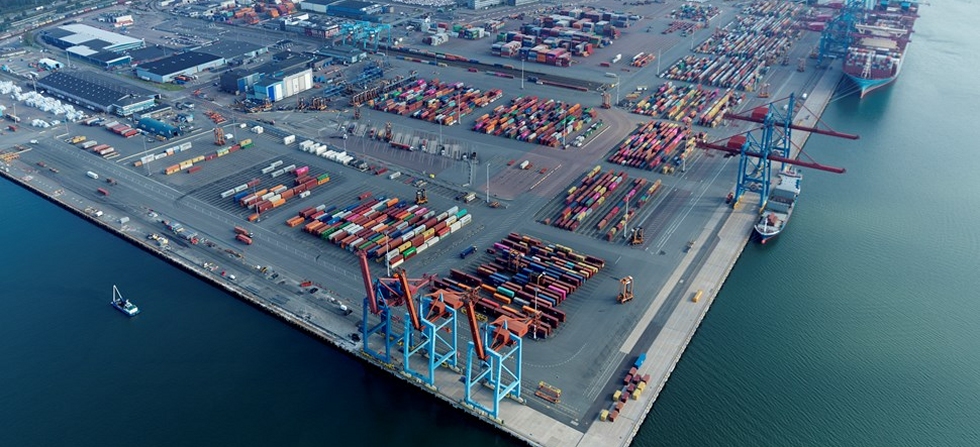
Short-sea Terminal to Be Opened at the Port of Gothenburg
March 29, 2021 - A new terminal service is due to commence at the Port of Gothenburg, dedicated to intra-European container transport. The terminal will be located at Skandiahamnen’s western quay and will be operated by APM Terminals.
“In the wake of the pandemic, new logistics patterns have evolved with goods owners moving parts of their global production system closer to Europe. Short sea is a growing segment, and we are pleased that APM Terminals is continuing to meet the needs of the market, and at the same time broadening the port’s overall service offering,” said Elvir Dzanic, Gothenburg Port Authority chief executive.
With short-sea handling focused on European destinations, for example suitable storage and transloading facilities close to the quayside are needed, to offer greater flexibility and a further incentive for transport purchasers to switch more intra-European freight from road to the more environmentally friendly sea alternative.
“We are proud to be able to expand our already extensive portfolio with a sustainable and competitive short-sea solution. We see that container traffic in Europe is growing in importance and it is a natural progression that we provide our customers with a service that offers even greater flexibility,” said Dennis Olesen, Managing Director at APM Terminals Nordic.
The terminal will be located at the Skandiahamnen western quay, which was recently renovated and reinforced in the lead-up to the Skandia Gateway fairway project. The area is currently being reviewed to determine what needs to be adapted, adjusted, or added to ensure the most efficient short-sea handling system possible.
“As a global player with strong links to the Nordic region and Europe, we already have good experience from short-sea solutions that we have rolled out previously. At present, we are working on all fronts to identify and tailor our solutions to match the needs of the Swedish market,” Dennis Olesen concluded.
Coastal and inland shipping also possible
It will also be possible to handle coastal and inland shipping at the new terminal. Loading and unloading of barges and smaller vessels that form the backbone of these modes of shipping have specific requirements that are currently being examined to ensure the best possible solutions can be put in place.
“Increasing domestic shipping is high on the government’s agenda and we are looking to support this. It is a classic example of the benefits of systems thinking, and it is a further addition to the range of services that we offer, giving us even more reason to call ourselves the ‘the no-limit port’,” said Elvir Dzanic.
SOURCE: Port of Gothenburg |
|
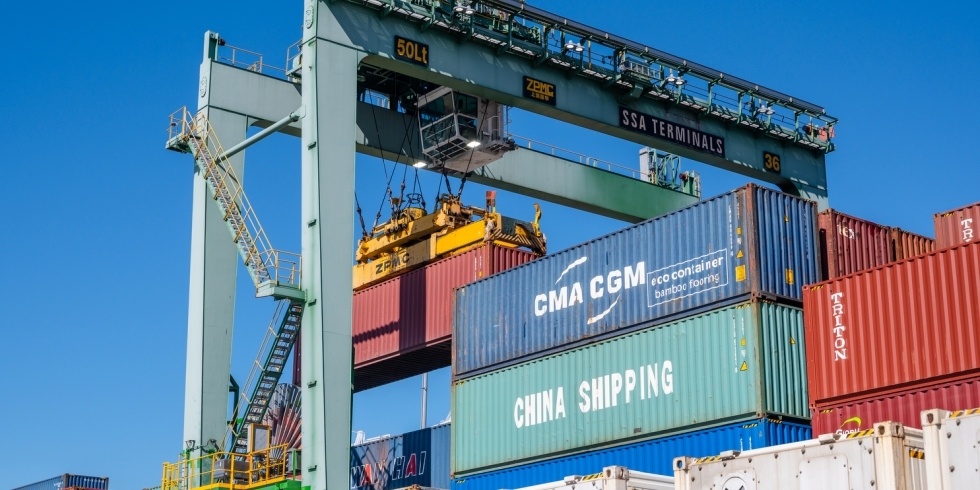
SSA Marine Puts Nine Electric Container Yard Cranes in Service at Port of Long Beach
March 9, 2021 - SSA Marine is now operating the first of nine electric container yard cranes at the Port of Long Beach’s Pier J (California), marking a significant milestone in a goal to transition to zero emissions terminal equipment by 2030.
The demonstration of the electric rubber tired gantry cranes is part of the Zero-Emissions Terminal Equipment Transition Project, which is funded in large part by a $9.7 million California Energy Commission grant. The Port, the CEC and Southern California Edison are partnering on the project to bring 25 vehicles that are zero- or near-zero emissions to three of the Port’s marine terminals and logistics truck provider Total Transportation Services Inc. to test their performance in a real-world setting.
“Imagine a port where a ship slows down on approach to reduce emissions, plugs into the electrical grid at berth instead of burning fuel to run vital systems, and is worked by zero-emissions cranes, yard vehicles and trucks,” said Port of Long Beach Executive Director Mario Cordero. “That’s our reality in Long Beach, and the goals of our tests and demonstrations are to eventually make it possible to do everywhere.”
“The future of the industry is zero emissions,” said Long Beach Harbor Commission President Frank Colonna. “The Port of Long Beach will continue to generate economic opportunity as we show that jobs and environmental sustainability can work together.”
“SSA Terminals is proud to partner with the Port to achieve our shared goal of implementing zero-emission cargo handling equipment,” said SSA Superintendent Scott Hainlen, the project coordinator. “We look forward to continuing this partnership with the Port as we explore all options to help do our part to continue to reduce our carbon footprint in Long Beach.”
In 2017, the ports of Long Beach and Los Angeles approved an update to their Clean Air Action Plan, setting a goal of transitioning all terminal equipment to zero emissions by 2030. Learn more at the website.
The Zero-Emissions Terminal Transition project is anticipated to annually reduce greenhouse gases by more than 1,323 tons and smog-causing nitrogen oxides by 27 tons. For more information about the project and associated initiatives, visit: www.polb.com/zeroemissions.
SOURCE: Port of Long Beach |
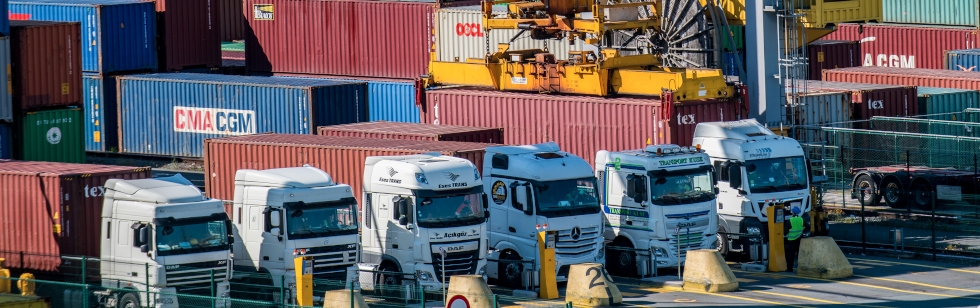
Port of Antwerp Says ‘Certified Pick Up’ Proceeding Smoothly
March 12, 2021 - The Port of Antwerp said that ‘Certified Pick up’ has been in use at the port of Antwerp since January 2021 and the new system is working well.
“The digital, safe and integrated solution for the release of containers is a long-term replacement for the current PIN code system. The new way of working guarantees a secure, transparent and optimised release process for incoming containers, which will then leave the port by rail, inland navigation or truck.” the Port said.
“Signing up to Certified Pick up is mandatory if you are involved in the container release process in Antwerp. This central data platform was developed by NxtPort. At present, nearly 90% of all the shipping companies and terminals in Antwerp have signed up to the system,” the Port added.
Transparency around container status
In this initial phase, Certified Pick up offers transparency around the status of your incoming container in the form of a series of "green lights". When all the lights in the application are on green, you can see at a glance whether the container is ready for collection. This improves operational efficiency for all the users involved.
PIN codes will be gone for good
Port of Antwerp has chosen a phased approach to guarantee the stable expansion of the system. In the next phase, the various chain partners will switch from the PIN code system to the new handling method with pick-up based on encrypted identification and authorisation data.
Truck drivers will pick up containers by identifying themselves digitally. PIN codes will no longer be used for inland navigation or rail, either. The use of Certified Pick up will be mandatory from then on. The legal framework is included in the Port Police Regulations.
SOURCE: Port of Antwerp |
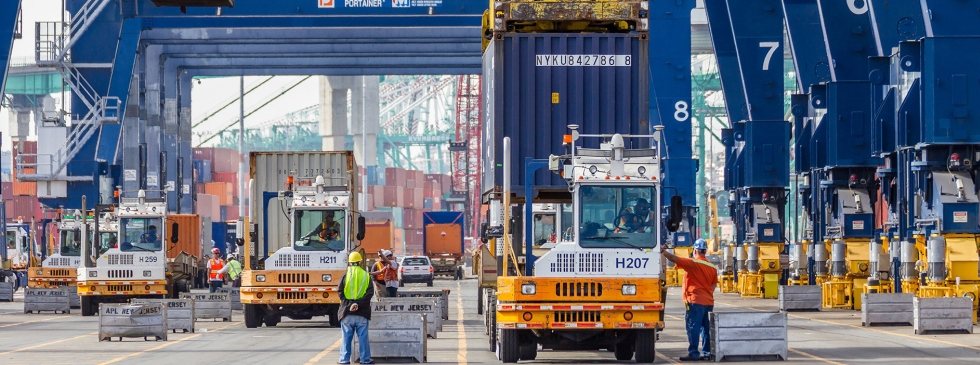
Port Of Los Angeles Launches New ‘Control Tower’ Data Tool for Tracking Cargo
Service provides real-time truck turn-time data and other metrics to boost advanced planning capabilities for Port stakeholders
March 1, 2021 - As part of its ongoing push to further digitalize the port supply chain and improve cargo efficiency and fluidity, the Port of Los Angeles has introduced a new “Control Tower” data tool — the third such instrument introduced by the nation’s busiest trade gateway in less than six months. The Control Tower offers real-time views of truck turn times, as well as other truck capacity management information, to help cargo owners, truckers and other supply chain stakeholders better predict and plan cargo flows.
“The Control Tower is a service and digital tool that will help get critical and reliable information to San Pedro Bay port stakeholders so that they can improve decision making and efficiencies,” said Port of Los Angeles Executive Director Gene Seroka. “We are currently the only port in North America offering this array of digital tools, but I’m optimistic that this type of data will eventually be more uniformly available at every node of the supply chain.”
Phase one of the Control Tower launch provides users current snapshots of turn times at all of the Port’s cargo terminals, updated continuously with GeoStamp data and broken down by historical daily and monthly averages. The Control Tower also provides recent and future trending volume data, as well as historical volumes and trends dating back to 2017, segmented by mode and specificity.
Developed in partnership with Wabtec, the Control Tower is being rolled out in phases, with more features added throughout 2021 based on user feedback and supply chain developments. Port stakeholders can sign up to use the Control Tower at: Tower.Portoptimizer.com.
“Data is a critical resource in moving goods across the supply chain and into the hands of consumers,” said Scott Holland, Vice President of Wabtec’s Network and Logistics business. “The Port Optimizer Control Tower is an important step in the journey to connect railroads, chassis providers, truckers, warehouse operators and others across the supply chain, and ensure cargo seamlessly flows in and out of ports. This system’s real-time and historical analytics will help the Port of Los Angeles community optimize their operations, relieve congestion stemming from increased global shipping traffic, and get products to people faster.”
The Control Tower builds on the data and success of the Port Optimizer™, the cloud-based secure digital portal of maritime shipping data created by the Port in 2017 to facilitate more efficient cargo flow through its terminals. Today’s Control Tower roll-out follows the launch of two other digital tools under the Port Optimizer umbrella in recent months: the Signal and Return Signal.
Launched this past September, the Signal data tool provides a three-week look at cargo coming into the Port of Los Angeles, with information updated daily. This information is now viewable via the Control Tower platform as well. The Return Signal tool introduced in November provides data that lets the trucking community know when and where to return empty containers to cargo terminals throughout the San Pedro Bay port complex. Return Signal data is updated every five minutes.
SOURCE: Port of Los Angeles |
Alabama State Port Authority Names Beth Ann Frisher as Chief Commercial Officer
Feb. 26, 2021 - Alabama State Port Authority announced that Beth Ann Frisher has joined the Port Authority’s senior management team as the new Chief Commercial Officer, effective February 18, 2021.
Ms. Frisher will be responsible for all commercial activities involving sales, marketing and real estate development.
“Beth stood out amongst a very impressive list of qualified individuals seeking to lead this critical position at the Authority,” said John Driscoll, Director and CEO of the Port Authority.
Prior to joining the Port Authority, Ms. Frisher served as the head of business development and international marketing at the Port of Oakland. Her experience also includes over 15years with AP Moller-Maersk in both Europe and North American directing sales and marketing, business process and pricing initiatives.
Ms. Frisher earned her Bachelor of Arts from Duke University and Master of Business Administration from the University of North Carolina at Chapel Hill.
The Alabama State Port Authority owns and operates the State of Alabama’s deep-water port facilities at the Port of Mobile, currently the 11thlargest U.S. Seaport by total trade and generating $25.4 Billion in economic value statewide.
SOURCE: Alabama State Port Authority |
|
|
|
<< first < Prev 11 12 13 14 15 16 17 18 19 20 Next > last >>
|
Page 17 of 31 |