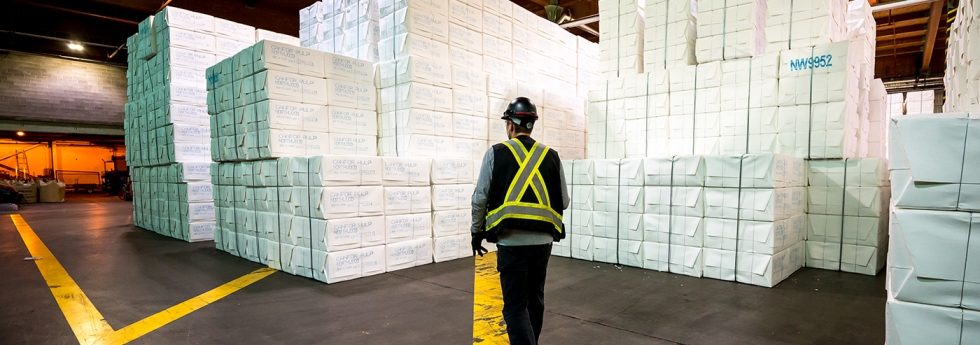
Canfor Pulp Reports Second Quarter 2024 Results
July 25, 2024 - Canfor Pulp Products Inc. ("CPPI") (TSX: CFX) reported its second quarter of 2024 results.
Overview
- Q2 2024 operating loss of $5.6 million; net loss of $6.3 million, or $0.10 per share.
- Strong global pulp pricing and moderate improvement in NBSK pulp unit sales realizations.
- Intercon NBSK pulp mill scheduled maintenance downtime completed as planned; restart delayed due to unforeseen recovery boiler repairs and start up challenges.
- Announced indefinite curtailment of one production line at Northwood NBSK pulp mill, driven by the decline in availability of economic fibre in the northern British Columbia region.
The Company reported an operating loss of $5.6 million for the second quarter of 2024, compared to an operating loss of $15.7 million for the first quarter of 2024. These results largely reflected an uplift in global pulp pricing, primarily in response to global pulp supply disruptions, and the correlated improvement in the Company's average Northern Bleached Softwood Kraft ("NBSK") pulp sales unit realizations. These factors were offset in part, however, by a decline in the Company's pulp production and shipments quarter-over-quarter, driven by extended downtime at its Intercontinental NBSK pulp mill ("Intercon") to address unforeseen recovery boiler repairs identified during the scheduled maintenance in May.
In May 2024, the Company announced the decision to indefinitely curtail one production line at its Northwood NBSK pulp mill ("Northwood") as a result of the continual decline in the availability of economic fibre in the northern British Columbia ("BC") region. The Company anticipates winding down this production line in August 2024. In connection with this indefinite curtailment, CPPI recognized restructuring costs of $5.9 million during the current quarter.
CEO Comments
Commenting on the Company's second quarter of 2024 results, CPPI's President and Chief Executive Officer, Kevin Edgson, said, "While our pulp business benefited from strong global pulp pricing this quarter, operationally, unanticipated downtime at our Intercon pulp mill limited our ability to take full advantage of this higher pricing environment and moderated our second quarter results. The decision to indefinitely curtail one line at our Northwood NBSK pulp mill was extremely difficult, however, necessary given the continuing fibre cost pressures and a difficult outlook for availability of economic residual fibre in BC. We regret the impact these decisions have on our employees, their families and the local community, and are working to support our employees through this transition. As we prepare for an orderly wind-down in August, we would like to thank our employees for their unwavering commitment and perseverance."
Second Quarter Highlights
Although global pulp producer inventories remained relatively balanced throughout the current quarter, the uplift in global softwood kraft pulp markets experienced at the end of the first quarter continued well into the second quarter, as global supply disruptions gave rise to an uptick in global pulp pricing. As a result, NBSK pulp list prices on orders from China, the world's largest consumer of pulp, saw steady increases throughout most of the period, reaching a 15-month high of US$825 per tonne in May, before declining in June, to end the quarter at US$810 per tonne. For the current quarter overall, average US-dollar NBSK pulp list prices to China were US$811 per tonne, an increase of US$66 per tonne, or 9%, from the previous quarter.
Pulp production was 130,000 tonnes for the second quarter of 2024, down 28,000 tonnes, or 18%, from the first quarter of 2024, primarily due to a reduction in operating days at Intercon. While the scheduled maintenance at Intercon was successfully completed as planned in early May, downtime was extended into early June to address unplanned repairs that were determined necessary following an inspection of Intercon's recovery boiler. The delayed restart resulted in pulp from Northwood being redirected to supply the Company's specialty paper facility.
Notwithstanding higher slush pulp costs (linked to the uplift in Canadian dollar NBSK pulp unit sales realizations), operating income in the Company's paper segment was $1.9 million, up $0.8 million from the previous quarter, largely reflecting moderately higher paper unit sales realizations, driven by an increase in global US-dollar paper pricing.
Outlook
Looking forward, global softwood kraft pulp market conditions are anticipated to soften through the third quarter of 2024 as global softwood pulp supply stabilizes, following disruptions in the first and second quarters of 2024, and as new hardwood capacity in China and Brazil is projected to come online. On the demand side, purchasing activity during the third quarter of 2024 is projected to dampen as the traditionally slower summer period is forecast to combine with reduced demand for paper products, particularly in China, further weakening pulp demand.
As a result of the aforementioned decision to wind down one production line at its Northwood pulp mill in August 2024, the indefinite curtailment will result in the reduction of approximately 300,000 tonnes of market kraft pulp annually. Consequently, the Company's results in the third quarter of 2024 will reflect the impact of this wind down on production, shipments and cost structure.
Looking forward, while the Company is focused on optimizing a sustainable operating footprint, improving operational reliability and closely managing manufacturing and fibre costs, it will continue to evaluate its operating conditions and will adjust operating rates at its pulp mills to align with economically viable fibre supply. These factors could also affect the Company's operating plan, liquidity, cash flows and the valuation of long-lived assets.
Bleached kraft paper demand is forecast to remain solid through most of the third quarter of 2024, after which a modest slowdown in demand is anticipated as global kraft paper inventories return to more normalized levels.
No major maintenance outages are planned for the third quarter of 2024.
Canfor Pulp Products Inc. is a leading global supplier of pulp and paper products with operations in the northern interior of British Columbia, Canada. Canfor Pulp operates two mills in Prince George, BC with a total capacity of 780,000 tonnes of Premium Reinforcing Northern Bleached Softwood Kraft ("NBSK") pulp and 140,000 tonnes of kraft paper.
SOURCE: Canfor Pulp Products Inc. |