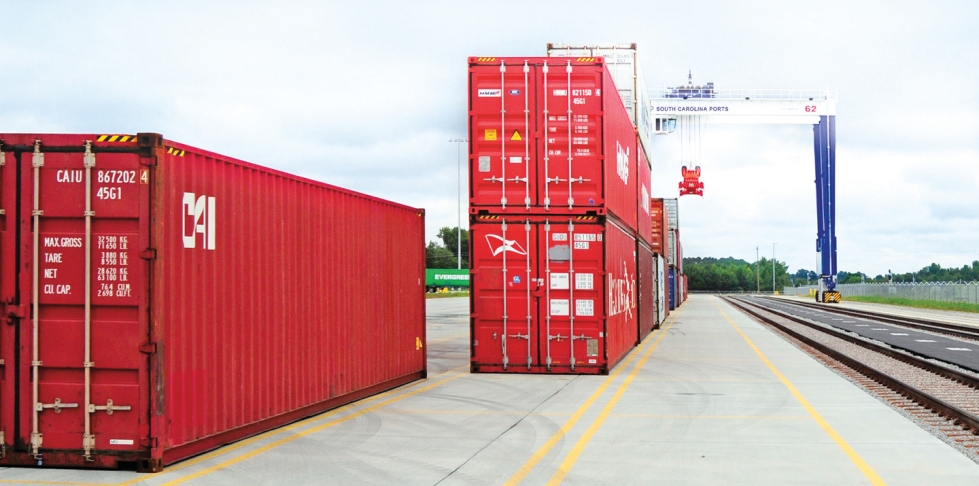
Smart Shipping Reduces Environmental Effects
The following story is from Domtar’s Newsroom
Sept. 15, 2021 - Providing products people around the world rely on every day involves not just manufacturing, but also millions of miles of transporting. By using smart shipping practices, Domtar has reduced the environmental effects of transporting its products.
In 2021, we will move about 240,000 pulp and paper shipments over the road. To get them to their destinations, drivers will travel more than 126 million miles, which is equal to about 5,100 trips around the equator.
Our products are also traveling by train. Nearly 1,120,000 tons of our pulp and paper will be packed on more than 16,000 rail cars in North America.
Over the last 10 years, we have circumvented more than 650,000 metric tons of greenhouse gas emissions through strategic planning that helps us get products moved as efficiently as possible while also limiting our impact on the environment.
“We have a sophisticated and cost-effective third-party distribution network to get products to customers,” says Debbie Campbell, Domtar’s director of transportation. “Yet we’re always looking at ways to improve efficiency and sustainability when it comes to transporting our products.”
Award-Winning Progress
Our smart shipping efforts have been recognized by both government agencies and our logistics partners. Since 2015, we have been a member of the U.S. Environmental Protection Agency’s SmartWay program, which helps companies advance supply chain sustainability by measuring, benchmarking and improving freight transportation efficiency.
Today, we’re one of just six companies based in South Carolina that are SmartWay-certified shippers. Launched in 2004, the voluntary program provides a comprehensive system for tracking, documenting and sharing information about fuel use and freight emissions. It helps companies identify and select more efficient freight carriers, transport modes, equipment and operational strategies to improve sustainability and lower costs associated with moving goods.
Earlier this year, we were one of several companies recognized by Canadian-based rail carrier CN for our efforts in reducing our environmental footprint and for being part of CN’s commitment to building a more sustainable future. Domtar was recognized as part of the EcoConnexions Partnership Program, which “celebrates companies who are committed to reducing their environmental footprint and being part of the climate solution.”
Three Keys to Smart Shipping
There are three main ways Domtar addresses sustainability through smart shipping:
Mode switch. We want to ensure that at any time, we are using the most efficient mode of transportation available, while mitigating as much carbon dioxide emission as possible. This may involve a mix of transportation modes (trucking, rail, shipping) — called intermodal shipping.
Route optimization. Switching modes often isn’t enough to move the needle in reducing carbon dioxide emissions. This is where smart routing technologies and smart production planning come into play. These smart shipping strategies not only help reduce the total miles we ship, but also the empty miles that don’t have a load. “We work hard with technology companies as well as our own internal optimization tools to help us reduce our shipment plans and empty miles,” Campbell says.
Engaging our partners. As a larger shipper that doesn’t own or operate its own transportation equipment, Domtar must work closely with transportation partners to help them implement initiatives to reduce carbon emissions. Examples include working to maximize truck and container volumes and optimizing product packaging and stacking arrangements. These efforts can reduce the number of trucks or trips necessary to transport our products.
Our geography also helps us. Most of our mills and converting sites are located near the markets they serve. Fewer miles to cover means less fuel burned and fewer emissions.
To take the next step in reducing our carbon emissions, Brian Kozlowski, director of environment and sustainability, believes maximizing our use of intermodal hubs in the coming years will be crucial.
For example, using the intermodal facility in Dillon, S.C., near our Marlboro Mill, we can load our products into a container and truck them fewer than 40 miles before they are lifted onto a train and brought directly to the port in Charleston.
This reduces the number of truck miles our products travel by more than 75 percent, resulting in fewer emissions, less congestion and less wear on the roads, Kozlowski says. Having seen these benefits at the Dillon facility, we continue to advocate for building additional intermodal facilities near our mills and converting centers to offer similar efficiency benefits to our customers around the globe.
Domtar makes products that people around the world rely on every day. We design, manufacture, market and distribute a wide variety of communication, specialty and packaging papers, market pulp and airlaid nonwovens. To learn more, visit: www.domtar.com.
SOURCE: Domtar |