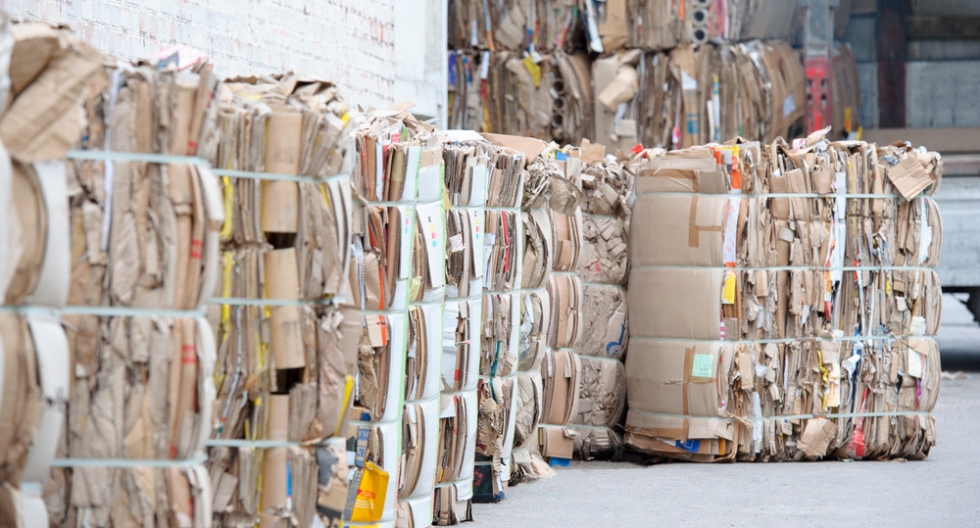
Port Tampa Bay Approves Lease to Celadon for Construction of Recycled Pulp Plant
March 29, 2021 - The Port Tampa Bay Board of Commissioners have approved an agreement with Celadon Development Corporation to lease 37 acres for the construction and operation of a paper fiber manufacturing plant. The plant will have significant economic and sustainability benefits generating up to 20,000 export containers per year (40,000 TEUs), creating approximately 100 jobs and involving a capital investment of $160 million during Phase One of the project.
The facility will receive and process mixed paper, corrugated cardboard and plastic products sourced in Florida to produce recycled pulp in sheets for export to Asia. Environmental and sustainability benefits include increased recycling, water reuse and reduction of greenhouse gases, saving over 1.8 million tons in carbon dioxide emissions.
Phase Two of the project will see the addition of a second production line that will double the plant’s capacity, increasing the output to 40,000 export containers per year (80,000 TEUs), resulting in a total capital investment approaching $400 million.
The site which is on Port Tampa Bay’s Hooker’s Point property is located alongside the Port’s container terminal which is also undergoing a significant phased expansion and is operated by Ports America under a long-term lease. The site is adjacent to the City of Tampa’s wastewater treatment plant with plenty of capacity to accommodate the project’s use of reclaimed water and wastewater needs.
“We are delighted to welcome Celadon to the Port Tampa Bay family,” stated Paul Anderson, Port Tampa Bay President & CEO. “This project will have hundreds of millions of dollars in generational economic impact.”
Raul Alfonso, Executive Vice President & Chief Commercial Officer for Port Tampa Bay, noted, “This project perfectly complements our container development strategy by generating export return loads heading back to Asia and filling containers which arrive with goods for retail and e-commerce distribution centers along the I-4 Corridor. With the Celadon manufacturing plant’s location right next to our container terminal, we expect great synergies and supply chain cost savings.”
Celadon Development Corporation LLC is a partnership between Nicollet Industries and Kamine Development Company, two leaders in green infrastructure and sustainable development.
Port Tampa Bay is Florida’s largest and most diversified port. Given its proximity to the rapidly expanding Tampa Bay/Orlando I-4 Corridor which has emerged as Florida’s Distribution Hub, Port Tampa Bay, and terminal operator Ports America are expanding container terminal facilities to keep pace with this growth. To learn more, visit: www.porttb.com
SOURCE: Port of Tampa Bay |
|
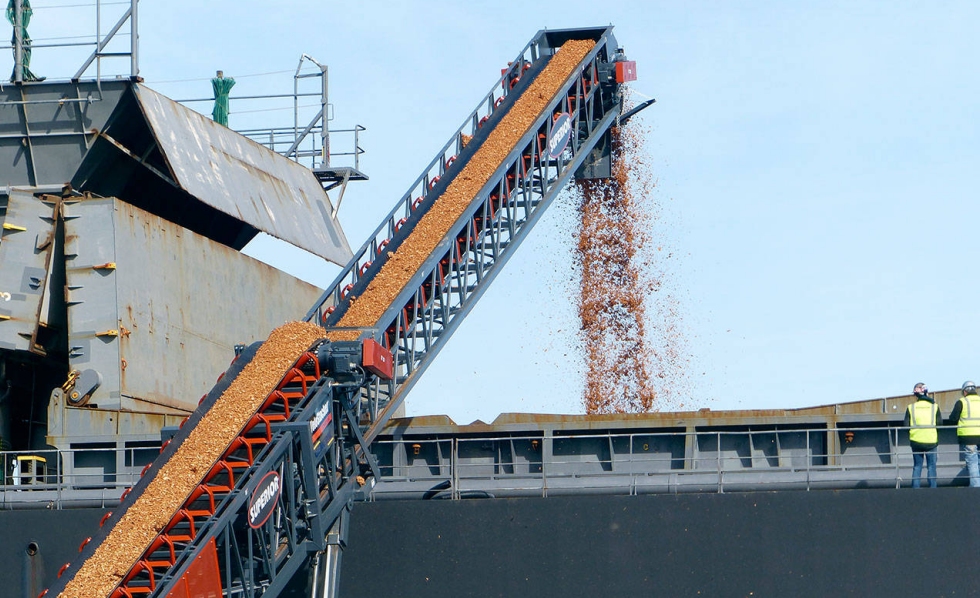
Chilean Wood Chip Exports Down 40% in 2020 as Asian Pulp Mills Increased Imports from Vietnam
March 26, 2021 - Wood chip exports from Chile plummeted in 2020, with shipments falling by over 40% from the first quarter to the fourth quarter. Only an estimated 450,000 odmt were shipped in the 4Q/20, the lowest quarterly volume since the 3Q/15, according to Wood Resource Quarterly. A combination of substantially reduced wood fiber consumption by Japanese pulpmills and an increased supply of lower-cost hardwood chips from Vietnam to Asian markets has contributed to the decline in demand for Chilean Eucalyptus chips in 2020.
Together with Vietnam and Australia, Chile has long been one of the primary wood fiber suppliers to the pulp industry in Japan. In 2013, the country was the number one source of wood chips to Japan, with a market share of 23%. However, the Chilean wood fiber supply in that market has diminished, and the percentage of total imports in the 4Q/20 was down to 11%.
The lower chip sales from Chile contributed to a five-year low in total wood chip shipments from Latin America in the 4Q/20. In just three years, the continent's export volume has fallen from 1.24 million odmt in the 4Q/17 to about 720,000 odmt in the 4Q/20.
Exports by Brazil have been relatively steady the past few years, ranging between 200,000-300,000 odmt per quarter.
Shipments from Uruguay, the third largest wood chips exporter on the continent, stopped entirely in the second half of 2020. The halt in shipments followed a long period when the country supplied pulp mills in Europe, predominantly Portugal, with between 500,000 and one million odmt of Eucalyptus chips annually.
The declining demand for hardwood chips by Asian pulp mills in 2020 has substantially reduced export prices (FOB) in Brazil and Chile, Wood Resource Quarterly said. The Latin American Wood Chip Export Price Index fell in the second half of 2020 to its lowest price in over ten years.
Wood Resource Quarterly is published by Wood Resources International, an internationally recognized forest industry consulting firm. For further information visit: www.woodprices.com.
SOURCE: Wood Resource Quarterly LLC |
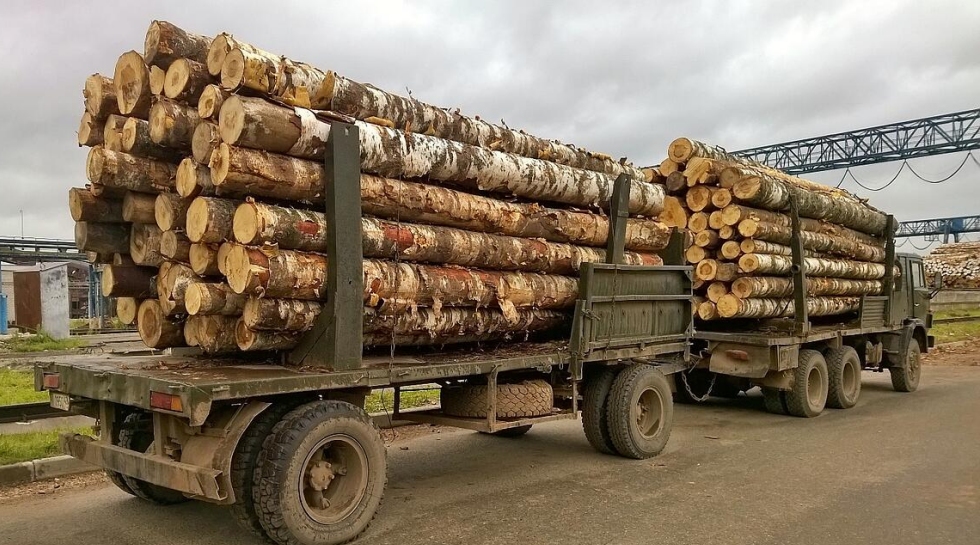
Russia’s Proposed Roundwood Export Ban Would Impact Global Trade
By Agris Melnis, Regional Sales Manager, Baltic Rim, Forest2Market
March 23, 2021 - Last fall, Russian president Vladimir Putin introduced legislation that would initiate a complete ban on exports of softwood and high-value hardwood logs from the country beginning January 1, 2022. Once established, this could also expand to include untreated or roughly processed green wood/lumber. This reduction in roundwood exports is intended to stimulate additional economic activity within Russia and help to mitigate illegal logging.
On January 1, 2021, an experiment on the traceability of timber turnover was launched, and will run through June 30, even though the ban is expected to be adopted as law in 2Q2021.
The global market for unprocessed timber will face significant shocks in the wake of such legislation resulting in a ban on Russian exports. By the end of 2020, Russia exported nearly 16 million cubic meters (m3) of timber, which represents almost 13% of globally traded roundwood.
China, which is the largest purchaser of logs from the far eastern region of Russia, will likely bear the brunt of this coming change. As a result, China will likely begin seeking out new suppliers in other regions such as Australasia, parts of Europe and the US. In the longer term, China is expected to shift a significant portion of its import volume from roundwood to sawn lumber.
Russia’s Forest Resources
Russia contains the largest area of natural forests in the world, covering 49% of the country’s landmass and 815 million hectares (2 billion acres), which is roughly 23% of the planet’s total forested area. Yet, much of the country’s forests are under threats of rapid deforestation. From 2001 to 2019, Russia lost approximately 65 million hectares (161 million acres) of relative tree cover, equivalent to an 8.5% decrease since 2000 and 18% of the global total. In 2018, Russia lost 5.6 million hectares (14 million acres) of tree cover. This rapid loss of forest resources could be impacting Russia’s desire to seek trade and policy solutions to help mitigate further deforestation.
According to statistics from the Russian Forestry Agency, wood harvesting in 2019 totaled 219 million m3, and export volumes were approximately 18 million m3.
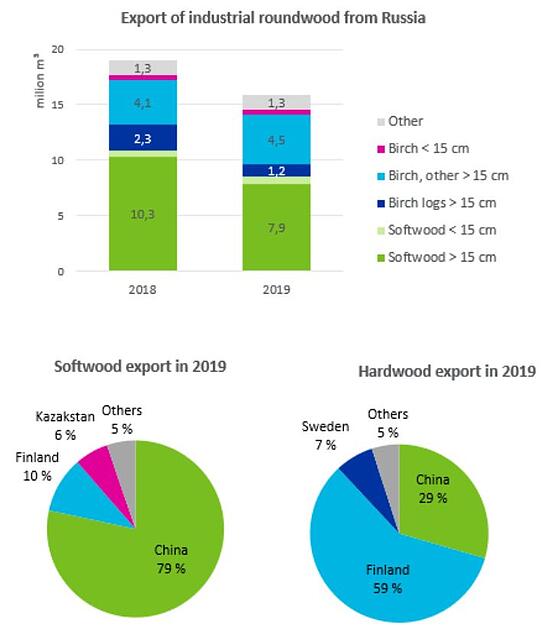
Russia is no stranger to using policy as a means to control its wood resources. In 2018, the government introduced export quotas for birch plywood logs for the first half of 2019. As a result, the total amount of exported birch logs in 2019 amounted to roughly 1.3 million m3, while just a year earlier this figure was approximately 1.9 million m3. As a result, in 2019, plywood production in Russia increased compared to 2018 as the wood raw materials stayed in-country and were used to expand manufacturing capacity. This legislative tactic has demonstrated effectiveness in the case of birch logs — but can such results be replicated for all Russian roundwood?
A ban on the export of all roundwood carries some additional challenges, including the risk of bankruptcy and the shuttering of small and medium-sized businesses focused only on this activity, which can also lead to a decrease in efficiencies throughout the industry, and an increase in tensions among forest industry stakeholders. To avoid such a predicament, the government is planning to launch a special modernization program through the Industrial Development Fund for small- and medium-sized businesses currently working in this space. This would help create loans for new equipment needed to help modernize and upfit existing facilities, as well as the establishment of new wood processing facilities.
The export ban will also affect other supply chain stakeholders related to roundwood production, including the transportation industry — particularly the railway sector — which is widely used for roundwood transportation.
A ban on Russian roundwood exports will certainly increase investment in the country’s wood processing sector and as a result, many local entrepreneurs are looking for new opportunities in Russia’s forest sector. However, such a ban could also carry the unintended consequence of damaging trade relations with some of its largest trading partners — most notably, China.
About the Author
Agris Melnis is Forest2Market’s Regional Sales Manager for European markets, including the Nordics, the Baltic States and Russia. In this role, Melnis serves as a supply chain expert and advisor to existing and prospective customers in the region and advises participants in the forest products industry on the use and integration of Forest2Market products and services into their business decisions. Agris has more than 20 years of experience in all phases of the wood fiber supply chain, from forest operations and procurement to product certification and export logistics.
SOURCE: Forest2Market |
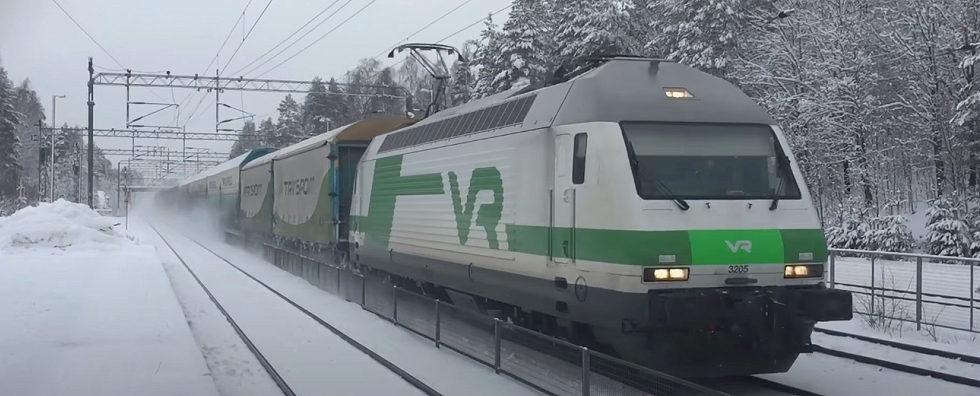
Metsä Group Selects VR Transpoint as Logistics Partner for Roundwood Transports to Kemi Bioproduct Mill
March 5, 2021 - Metsä Group has chosen VR Transpoint as the logistics partner for roundwood transports to the bioproduct mill under construction in Kemi. This decision was based on more than two years of strategic cooperation during which an effective and environmentally friendly overall solution was designed for the transports. Annually, five million cubic metres of wood will be transported to the mill by rail, which means that an average of nine trains will arrive at the mill every day.
The number of wood transports by rail will be increasing significantly in Finland from 2023 onwards when the bioproduct mill in Kemi is commissioned. This means annual deliveries of more than five million cubic metres of wood, for which Metsä Group has chosen VR Transpoint as its transport partner. The logistics solution has been fine-tuned in close cooperation already for more than two years.
“We appreciate our long-term partnership with VR Transpoint and offer them a further opportunity to grow by supplying wood to the Kemi bioproduct mill,” said Juha Mäntylä, COO, Metsäliitto Cooperative. “Railway transports play a significant role in the Kemi bioproduct mill’s wood supply, which requires this new, effective operating model.”
VR Transpoint is enabling a major investment of the forest industry for the second time — Metsä Group chose VR Transpoint as its partner also for the pulp transports of the Äänekoski bioproduct mill in 2016.
Martti Koskinen, Senior Vice President at VR Transpoint, explained, “The efficiency of transports and smooth flow of traffic are key factors when trying to attract major investments such as a bioproduct mill to our country. Finland is located far from the densely populated markets, so we have to catch up with more efficient logistics. We have now managed to create a solution in which the operations of the mill and railway transports are combined seamlessly.”
Wood is transported from longer distances, but with considerably fewer emissions
Due to the increased use of wood, it must be transported from wider areas, from north and south of Kemi, but these transports are done with considerably fewer emissions.
Although the distance travelled by the wood deliveries increases, emissions are reduced by 20% per cubic metre due to effective railway transports, Metsä Group said.
In practice, eight to ten trains will arrive at the Kemi bioproduct mill every day. The efficiency of the transport system is based on perfectly fine-tuned wagon rotation — the time between two consecutive loadings, including all the stages, takes only half the time of an average wood transport.
Rolling stock investments enhance delivery reliability
Due to the new contract, VR Transpoint is investing in approximately 200 new roundwood wagons. The bioproduct mill’s railway transports will require a total of more than 400 wagons. The newest electric and diesel locomotives will be used as the tractive stock. The new electric locomotives can handle loads of up to 2,500 tonnes, which means approximately 20–25% more wood per train.
Kemi Mill Project
Metsä Group is investing EUR 1.6 billion to build a bioproduct mill to replace its current mill in Kemi, Finland. The new mill will produce some 1.5 million tonnes of softwood and hardwood pulp per year, as well as many other bioproducts.
SOURCE: Metsä Group |
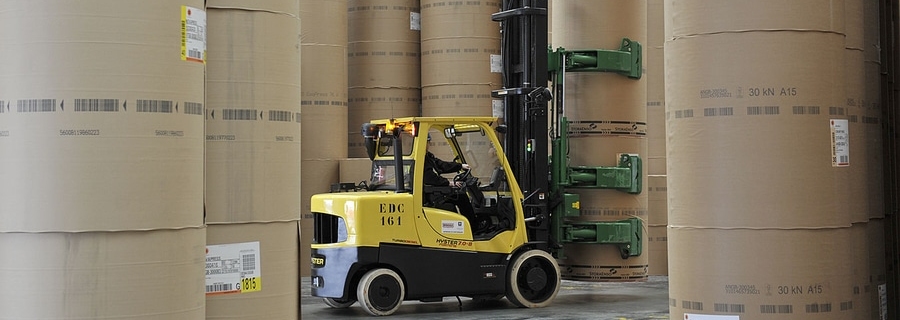
Scaling up Digital Solutions to Improve Warehouse Safety with Anti-Collision Program
By Sami Karttunen, Senior Manager for Supply Chain Logistics, Stora Enso
This post appears courtesy of Stora Enso, a leading global provider of renewable solutions in packaging, biomaterials, wooden construction and paper. The company employs some 23,000 people and has sales in more than 50 countries.
February 2021 - In environments where people and heavy machines co-exist there is always an imminent risk of accidents. As a company, we have the responsibility to take every measure we can to avoid those risks and ensure that each colleague gets home safe every day. In this blog, I will share my experience of how we in Stora Enso have leveraged digital technology to avoid accidents in our warehouses, as well as how digital solutions is paving the way to further improve safety in the future.
We are today undertaking the first company-wide global roll out of a digital solution in our mills. The digital solution in scope is called ‘Warehouse Anti Collision solution’ and does just what the name indicates — it helps humans and machines to avoid collisions in our warehouses. The goal is now that the solution will be implemented in 64 warehouses in seven countries by the end of 2021.
But before I continue, let me first take you back to where it all started. One could safely say that our warehouses are vibrant environments where employees co-exist with heavy machines like forklifts and trucks. Throughout the day, raw materials from suppliers are unloaded in the warehouse and finished products are loaded to be shipped to our customers. In 2016, a discussion was raised around what we could further do to avoid potentially dangerous collisions and accidents between humans and machines in these warehouse environments. Together with my team I screened through different potential solutions already existing in Stora Enso, but came to the conclusion that we needed to create something entirely new to fulfill the need.
Through our Stora Enso Digitalisation Fund we received funds to start the project of setting up a proof of concept of what would later become the Warehouse Anti Collision solution. A handful potential technical partners were evaluated to see if we could continue to build and co-create around their products. In the end, a company which had previously built alarm solutions for cross walks and railroad crossings was selected as our partner.
Together we started in small scale to test and roll out the new solution in our Finnish mill Imatra. The solution comprises detectors which employees carry, and other detectors installed on vehicles, like for example forklifts. When the two detectors come close enough to each other, an alarm goes off. Throughout the project, our employees have been highly involved in testing and giving feedback on the solution. Through the testing we made early discoveries — for example, the alarm signals needed tuning since they were irritatingly loud, and the radio signals needed to be strong enough to penetrate objects such as paper rolls.
As the project proceeded, important enhancement areas of the solution were identified. The detectors could also be configured to prevent unauthorized people enter restricted areas — only people carrying a detector should be able to enter. Moreover, what if we could decrease the number of unnecessary alarms going off if we could configure the detectors to work differently in specific safety zones? We solved this challenge by programming the detectors to sense when a human is inside a safety zone and thus deactivating the alarm signal, while also ensuring that a vehicle cannot enter the safety zone at all.
Reflecting on this journey, I am most proud that the implementation of this solution has greatly reduced the risk of accidents in our warehouses. Since the solution was implemented in Imatra, we have had no accidents or even close calls to accidents between humans and machines in our warehouse. I am also very keen to see what the future holds for our global roll outs of digital solutions.
2021 and forward is going to be the time of truly scaling out digital technology in our mills and sites cross the company to increase safety. As an example, we are now focusing on scaling out the IoT hand valve sensors during the coming years. These sensors further help us ensure that we have control over the fluids in our mill systems to avoid accidents of leakages. Another example is a mobile app currently being scaled out to support employees with social distancing during the Corona pandemic.
These are only a few examples of what we are doing. And looking even further into the future, many of the digital solutions we are working on for our mills are also indirectly going to increase safety for our employees. For example, when we automate processes, or ensure proactive rather than reactive maintenance with the help of analytics and AI, we also reduce the risk of humans becoming the subject of an accident. Digitalisation will help us ensure we deliver on our goal of every colleague getting home safe every day.
About the author: Sami Karttunen joined Stora Enso in 2004 and started out as responsible for developing the rail logistics from wood terminals to mills, and has also had the role of production engineer for Imatra mills. Most recently he has worked as a Senior Manager for Supply Chain Logistics in Finland. Sami was also the initiator and project manager of the digital Warehouse Antti Collision Solution.
SOURCE: Stora Enso |
|
|