International Paper to Sell Global Cellulose Fibers Business for $1.5 Billion; Close Savannah Containerboard Mill
Aug. 21, 2025 - International Paper today announced a series of strategic changes to achieve an advantaged cost position, deliver a superior customer experience and maintain a high relative supply position as part of its ongoing transformation journey.
Agreement to Sell Global Cellulose Fibers Business
International Paper has reached a definitive agreement with American Industrial Partners (AIP) to sell its Global Cellulose Fibers (GCF) business for $1.5 billion, subject to closing adjustments, including the issuance of preferred stock with an aggregate initial liquidation preference of $190 million. The Company previously announced the decision to review strategic alternatives for its GCF business last fall, as part of the Company's strategy to focus on sustainable packaging solutions. The transaction is expected to close by the end of the year, subject to regulatory approvals.
"GCF is a strong business, and I'm pleased to see it transitioning to AIP, which is focused on investing in and growing industrial businesses," said IP Chief Executive Officer Andy Silvernail. "Over the past few months, GCF has done the hard work of aligning resources with its most strategic customers, implementing an 80/20 mindset, and creating a simplified and focused portfolio. These actions, combined with its talented and committed team made it an attractive investment for AIP to enter the pulp market and have positioned GCF for long-term success under new ownership."
"GCF is well-positioned for future growth, supported by its large and sustainable wood basket, durable end markets, industry leading quality and innovation, long-term customer relationships, deeply knowledgeable employees, and well-invested facilities," said Rick Hoffman, Partner at AIP. "We look forward to partnering with GCF Senior Vice President Clay Ellis and the rest of the talented and tenured management team to implement their growth vision."
The GCF business creates safe, high-quality pulp for a wide range of applications like towel and tissue products, diapers, feminine care, incontinence and other personal care products that promote health and wellness. In addition, its specialty pulp serves as a sustainable raw material used in construction materials, paints, coatings and more. GCF generated $2.8 billion in revenue in 2024 and has 3,300 employees globally, with nine manufacturing facilities and eight regional offices.
Strategic Changes to Packaging Solutions Business in North America
International Paper's packaging business in North America has initiated a number of actions to enhance its ability to serve and grow with customers while improving its manufacturing footprint, including:
- Investment of $250 million to convert the #16 machine at the Riverdale mill in Selma, Alabama to produce containerboard
- The permanent closure of the Savannah, Georgia containerboard mill, the Savannah, Georgia packaging facility, Riceboro containerboard mill and Riceboro Timber and Lumber
These changes will impact approximately 1,100 hourly and salaried positions. International Paper is committed to supporting affected employees through this transition. The Company will offer severance packages, along with outplacement assistance for eligible employees, to support them during this transition.
"We understand how deeply these decisions affect our employees, their loved ones, and the surrounding communities," said Tom Hamic, Executive Vice President and President of International Paper's North America Packaging Solutions business. "We are committed to supporting both our employees and customers as we navigate this transition.
"While difficult, these decisions are essential to positioning International Paper for long-term success, enabling us to focus on the geographies, customers, and products where we can create the most value," Hamic added. "Our investment in the Riverdale mill reflects our commitment to delivering high-quality, reliable service while strengthening our advantaged cost position."
The Riverdale conversion is expected to be completed by the third quarter of 2026. The Riceboro and Savannah mills will shut down in phases by the end of September 2025, and the Savannah packaging facility will also cease operations by the end of September. These combined changes will result in a net reduction of the company's annual containerboard capacity by approximately one million tons.
International Paper (NYSE: IP; LSE: IPC) is the global leader in sustainable packaging solutions. With company headquarters in Memphis, Tennessee, USA, and EMEA (Europe, Middle East and Africa) headquarters in London, UK, IP employs more than 65,000 team members and serves customers around the world with operations in more than 30 countries.
SOURCE: International Paper |
|
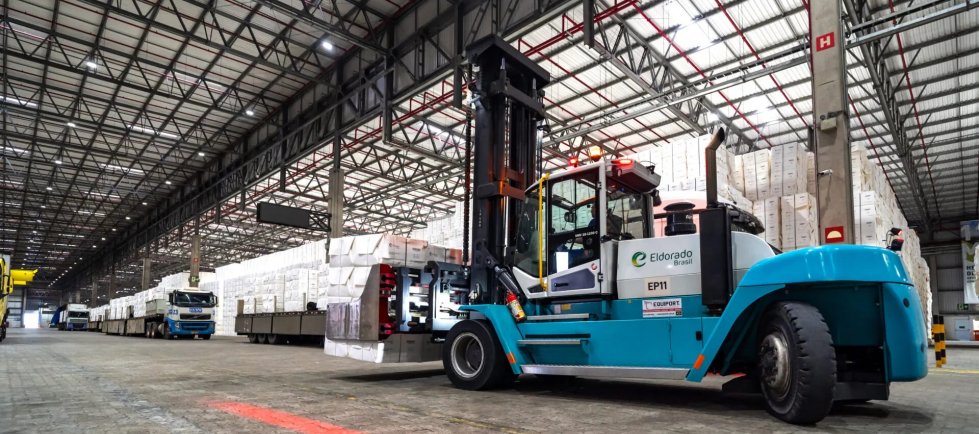
Eldorado Brasil's EBLog Terminal Celebrates 2 Years with International Recognition
Aug. 11, 2025 - Eldorado Brasil's EBLog Terminal celebrates its second year of operations by achieving important international certifications: ISO 9001 (Quality Management), ISO 14001 (Environmental Management), and ISO 45001 (Occupational Health and Safety). These certifications attest to the terminal's compliance with the highest international standards of quality, safety, and environmental responsibility. Furthermore, they reinforce the company's position as a benchmark in port logistics and in the global pulp market, which is increasingly demanding in terms of ESG criteria.
Although EBLog is celebrating two years of operation, Eldorado Brasil's presence in the Port of Santos dates back further. Since 2015, the company has operated in the port region through the former Rishis Terminal, established to meet the company's pulp export needs.
"EBLog was a milestone in this journey and is part of the company's consolidated strategic planning, focused on the future of port logistics and the business," says Flávio da Rocha Costa, Logistics Director of EBLog at Eldorado Brasil Celulose.
Located in the pulp and paper cluster of the Santos port region, EBLog is currently one of the most modern terminals in the world. The certifications, contractually stipulated by the port area lease to occur by February 2026, were brought forward by eight months.
Marcelo Falcão, Logistics Manager at Eldorado Brasil Celulose's EBLog, added, "Thanks to our team's efforts, we've carried out rigorous work with adjustments, training, and routine standardization, always guided by the same commitment that Eldorado has throughout its production chain. Achieving these ISO certifications places us at a high level of global competitiveness, which is very significant considering that Eldorado exports approximately 90% of its pulp to over 40 countries.”
Each certification plays a fundamental role in the business. ISO 9001 ensures process standardization, continuous improvement, and a focus on customer satisfaction. ISO 14001 establishes practices for controlling and reducing environmental impacts, encouraging sustainability.
Finally, ISO 45001 guides the structuring of risk prevention systems in the execution of tasks, enhancing the safety and well-being of all employees.
Eldorado Brasil Celulose, a J&F Group company, produces 1.8 million tons of high-quality pulp per year. In Santos, São Paulo, it operates EBLog, one of the most modern port terminals in Latin America, exporting its product to over 40 countries.
SOURCE: Eldorado Brasil Celulose |
Ence Reports Sales of Specialty Pulps Climb to 32% of Pulp Sales in First Half of 2025
Aug. 11, 2025 – Spanish pulp and paper producer Ence [on July 22] presented its results for the first half of the year, marked by falling pulp prices and uncertainty stemming from tariffs.
During this period, the company has continued to focus on its transformation strategy toward becoming a producer of higher-value-added specialty pulps, a substitute for long-fiber pulp, which will position it as one of the most competitive producers in this market. This is in addition to its commitment to non-conventional renewable energy, through new developments in biomethane and renewable industrial heat.
For its part, and during the second quarter of 2025, Ence has managed to reduce its average cost per ton of cellulose (cash cost) to 488 euros, which represents an improvement of 22 euros/ton compared to the previous quarter, thanks to the continuous improvement in operational efficiency and energy optimization initiatives.
Ence's Fluff Pulp to Replace Long-fiber Pulp
Specialty pulps continue to gain prominence within the company's commercial mix, already reaching 32% of total Pulp sales in the first half of the year, compared to 23% in the first half of 2024.
This development reflects Ence's firm commitment to higher value-added products and will be reinforced in the fourth quarter of the year with the start-up of the new fluff pulp production line for the absorbent hygiene products market. With this special type of pulp, Ence will be one of the most competitive producers in this market compared to long-fiber producers.
Financial Results
Ence recorded revenues of EUR 192 million in the second quarter, a 3% increase over the previous quarter. This figure was driven by higher sales volumes in both the Pulp business (with 243,000 tons, 12% more than the previous quarter, when Navia was shut down) and the Energy business (with 303 GWh, a 9% increase over the previous quarter), which helped mitigate a weak sales price environment.
Focused on the first half of 2025, the Group has completed two sales transactions with the accreditation of 191 million Energy Saving Certificates (CAEs) (equivalent to savings of 191 GWh) and 61 million CAEs (equivalent to savings of 61 GWh), respectively, with their transfer price, net of acquisition costs, of 30 million euros and 10 million euros, respectively.
In the first half of 2025, the company recorded net attributable profit of -6.9 million euros, impacted by the decline in pulp prices.
Recovery Expectations
The average raw short staple fiber price (BHKP) in Europe was $1,177 per ton between April and June (compared to a peak of $1,218/t reached in April) and, in July, stood at $1,060/t, below the industry's marginal production cost. The restocking process should drive a price recovery once tariff uncertainties are overcome.
SOURCE: Ence (Energía y Celulosa) |
Metsä Board Launches Programme to Improve Profitability and Cash Flow
Aug. 5, 2025 - Metsä Board, part of Metsä Group, has experienced a prolonged period of unsatisfactory profitability and cash flow performance. Intensified competition and more cautious consumer behaviour have reduced demand for paperboard packaging. Additionally, high wood raw material costs and the weak development of the pulp market have negatively impacted the company’s performance and competitiveness.
In response to the changing market environment, the company is accelerating growth and strengthening its services in Europe by leveraging its strong market position, leading sustainability performance, and expertise in developing material-efficient, safe, and recyclable packaging solutions for customers. This development is further supported by the tightening requirements for packaging of the EU Packaging and Packaging Waste Regulation (PPWR).
The company’s objective is to maintain a strong market position in the U.S. and drive growth especially through existing customer relationships. Over the past ten years, Metsä Board’s growth has been strongly focused on the U.S. market. Increasing global uncertainty and import tariffs have together temporarily reduced Metsä Board’s paperboard deliveries to the United States. Due to growth-related uncertainties, new growth efforts are also being directed toward other markets.
Metsä Board’s Board of Directors [on July 31] decided to launch a cost savings and profitability improvement programme, targeting an annual EBITDA increase of EUR 200 million. The programme consists of cost savings (EUR 100 million) and profitability improvement (EUR 100 million). Implementation will begin immediately by initiating project planning and execution under a new management structure. Progress will be reported regularly.
"We must take immediate actions to improve our profitability and competitiveness,” said Esa Kaikkonen, CEO, Metsä Board. “Our cost structure must be adjusted to reflect current market conditions. Before launching the programme, we conducted a thorough analysis of our operating environment and our strengths. Our leading position in high-quality, fresh fibre-based packaging solutions, long-term customer relationships, and committed personnel form a strong foundation for profitability improvement."
The programme is expected to improve comparable EBITDA by EUR 100 million in 2026, with the majority of the impact in the second half of the year. The remaining impact is expected to be realised by the end of 2027. Additionally, the closure of the Tako mill and efficiency improvements at the Kyro mill are expected to contribute approximately EUR 30 million in annual EBITDA improvement starting from Q4 2025.
In addition to delivering cost savings, the programme sharpens commercial focus by redefining key customer segments and strategically aligning sales efforts to support profitable growth.
Product development will focus on meeting evolving regulatory requirements, particularly in the fast-growing food and foodservice packaging segments, healthcare, and other strongest growing brand segments. Supply chain efficiency will be improved by streamlining the product portfolio and reducing complexity.
To strengthen cash flow, Metsä Board aims to release at least EUR 150 million in working capital by the end of 2025. The company will conduct a critical review of ongoing investment pre-engineering projects and its ERP programme and provide an update on them latest in its interim report for January–September 2025. In addition, Metsä Board will update its strategy and renew its financial targets – currently ROCE >12% and net debt to EBITDA < 2.5 – by the end of first quarter of 2026.
Metsä Board is a producer of lightweight and high-quality folding boxboards, food service boards and white kraftliners.
SOURCE: Metsä Board |
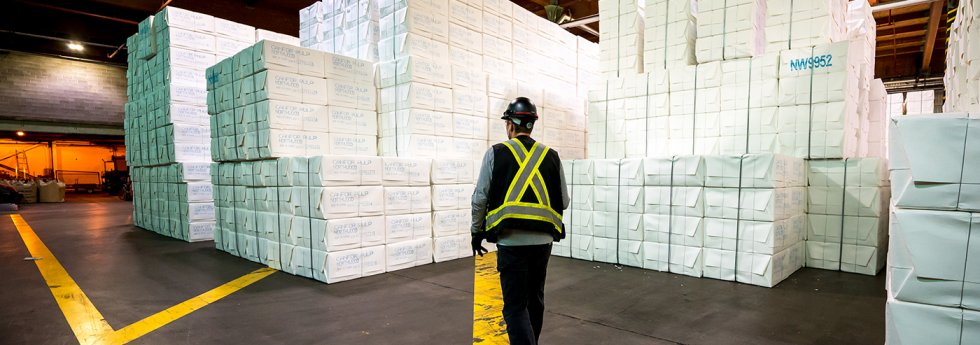
Canfor Pulp Reports Second Quarter 2025 Results
Aug. 1, 2025 - Canfor Pulp Products Inc. on July 31 reported its second quarter of 2025 results. The company reported an operating loss of $5.3 million for the second quarter of 2025, compared to operating income of $10.8 million for the first quarter of 2025. After adjusting for a $2.9 million inventory write-down in the current period, the company's operating loss was $2.4 million for the second quarter of 2025. These results were largely driven by a decline in both the company's average Northern Bleached Softwood Kraft ("NBSK") pulp and paper unit sales realizations in the current quarter and, to a lesser extent, an uplift in pulp unit manufacturing costs.
Commenting on the second quarter performance, CPPI's President and Chief Executive Officer, Stephen Mackie, remarked, "Our results for the second quarter of 2025 were strongly influenced by persistent global economic uncertainty, significantly impacting global pulp and paper market fundamentals. We anticipate these market pressures to continue throughout the third quarter. We are closely monitoring these external factors but continue to remain focused on optimizing areas within our control, including improving safety, reliability, productivity and cost structure."
Second Quarter Highlights
Global softwood pulp markets experienced downward pressure throughout the second quarter of 2025, primarily driven by weak demand from China, largely tied to the impact of new trade policies between China and the US, as well as general global economic uncertainty. As a result, US-dollar NBSK list prices to China, the world's largest pulp consumer, started the quarter at a high of US$798 per tonne, before declining steadily throughout the period, ending June at US$690 per tonne.
For the current quarter overall, US-dollar NBSK pulp list prices to China averaged US$734 per tonne, down US$59 per tonne, or 7%, from the prior quarter. As a result of weak demand, global softwood pulp producer inventories climbed significantly through the second quarter of 2025 to well above the balanced range, ending May at 46 days of supply, an increase of 8 days compared to March 2025. Market conditions are generally considered balanced when inventories are in the 32-43 days of supply range.
Canfor Pulp's average NBSK pulp unit sales realizations experienced a modest decline compared to the previous quarter, primarily reflecting US-dollar NBSK pricing pressure in China combined with a 3 cent, or 4%, stronger Canadian dollar. These factors, however, were moderated in the current period by an uptick in US-dollar pricing to other global regions, coupled with a favourable lag in the timing of shipments versus orders. As a result, the full impact of weak US-dollar China list prices towards the end of the second quarter will not be evident in the Company's average NBSK pulp unit sales realizations until the third quarter of 2025.
Pulp production was 102,000 tonnes for the second quarter of 2025, down 2,000 tonnes, or 2%, from the first quarter of 2025, primarily due to minor operational disruptions in the current period.
Operating income in the company's paper segment was $1.5 million, compared to $5.4 million in the previous quarter, largely driven by a slight decline in North American US-dollar paper pricing combined with the stronger Canadian dollar in the current period.
Outlook
Looking forward, global softwood kraft pulp market conditions are anticipated to remain weak throughout the third quarter of 2025 as purchasing activity, particularly from China, is forecast to be soft through the traditionally slower summer period, despite the announcement of market curtailments from some Nordic pulp producers. As a result, global pulp producer inventories are forecast to remain well above the balanced range through the third quarter of 2025.
The company continues to actively monitor developments in the trade relationship between Canada and the United States. In the event that tariffs are imposed on US pulp and paper shipments, the Company has mitigation strategies intended to largely offset potential impacts.
The subdued demand for bleached kraft paper in North America observed at the end of the first quarter and throughout the second quarter is anticipated to persist into the third quarter of 2025. This outlook is principally attributable to the ongoing uncertainties related to Canada-US trade relations, as well as general global economic pressures.
A minor scheduled maintenance outage will take place during the third quarter of 2025 at Canfor Pulp's Intercontinental NBSK pulp mill and at its paper machine. This maintenance outage is projected to reduce both NBSK market pulp production and paper production by 2,000 tonnes each.
Canfor Pulp Products Inc. is a leading global supplier of pulp and paper products with operations in the northern interior of British Columbia ("BC"). Canfor Pulp operates two mills in Prince George, BC with a total capacity of 780,000 tonnes of Premium Reinforcing Northern Bleached Softwood Kraft ("NBSK") pulp and 140,000 tonnes of kraft paper.
SOURCE: Canfor Pulp Products Inc. |
|
|