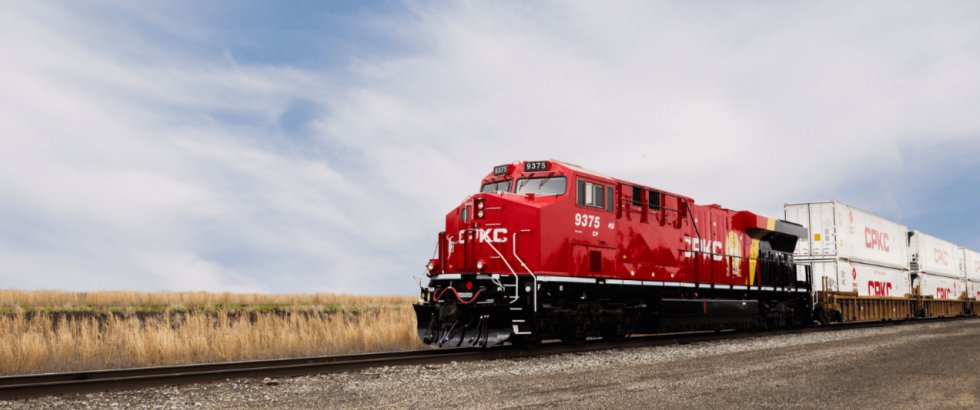
Unifor Members of Local 101R at Canadian Pacific Kansas City Railway Vote in Favor of Strike Action
Jan. 14, 2025 - Unifor members of Local 101R at Canadian Pacific Kansas City Railway (CPKC) have voted overwhelmingly in favour of strike action, with 99% of members voting in support.
"This strike mandate shows the strength and determination of CPKC workers to achieve a fair deal," said Unifor National President Lana Payne. "Members are united in their demands for job security and work ownership, fair wages, and improved working conditions."
The vote authorizes the union to initiate strike action if a deal is not reached by 12:01 a.m. EST on January 29, 2025.
"CPKC workers play a critical role in Canada's transportation network. Our union will stand firm to ensure their contributions are respected through an approved collective agreement," said Payne.
Negotiations with CPKC are set to resume in Calgary from January 24 to January 29, where the union's bargaining committee will continue its efforts to secure an agreement that meets the needs of all members.
Unifor represents more than 1,200 members at Local 101R who work in mechanical shops, inspecting and maintaining CPKC's fleet of locomotives and freight cars, and ensuring the railway's equipment is safe and operational.
Unifor is Canada's largest union in the private sector, representing 320,000 workers in every major area of the economy.
SOURCE Unifor |
|
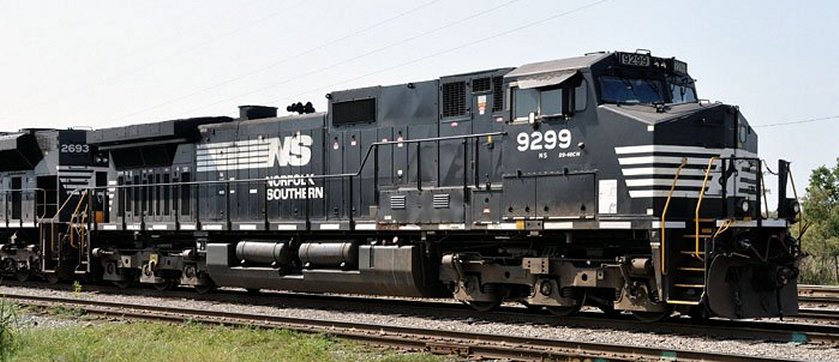
Norfolk Southern to Invest Over $200 Million in 3B Corridor Serving Alabama
Aug. 13, 2024 - Norfolk Southern is investing to grow capacity on a key rail line in the state of Alabama, the 3B Corridor, which connects markets in northern and central Alabama to the Port of Mobile and destinations worldwide. The more-than $200 million investment positions the line to accommodate expected growth in several sectors as the Southeast progresses as an economic powerhouse for the US economy.
The 3B Corridor is strategically aligned with the Port of Mobile, which contributes $85 billion in annual economic value to Alabama. The corridor represents an important segment of Norfolk Southern's annual traffic, serving critical industries like agriculture, automotive, chemicals, forestry, and steel. The investments are expected to yield immediate returns when they begin to come online in 2025.
"Together with our customers, we are anticipating where markets are heading, and positioning to deliver on their supply chain needs now and into the future," said Norfolk Southern President and CEO Alan H. Shaw. "These investments will bring immediate returns as they make rail an even more competitive part of our nation's supply chain and expand our customers end-to-end solutions."
The project involves a mix of terminal and track-based infrastructure improvements, including capacity projects in central and southwest Alabama, customer-specific projects in north Alabama and locations north of Mobile, yard upgrades in Wilton and a series of grade crossing improvements throughout the region.
"We are grateful to Norfolk Southern for these investments in our state and for their support of our existing industries," said Secretary of the Alabama Department of Commerce Ellen McNair. "This is proof that our open for business approach is attracting growth in our state among world-class businesses looking to locate or expand their operation. We look forward to the positive impact these enhancements will have on Alabama's economic competitiveness and on the nation's supply chain more broadly."
Norfolk Southern noted that a customer, Packaging Corporation of America, recently expanded its paper mill located along the corridor, partnering with Norfolk Southern on the project to enhance efficiencies for both companies.
Ross Corthell, PCA’s Vice President, Transportation, explained, "Without Norfolk Southern's investment in the region, we would not have been able to maximize the opportunity to ship more volume via rail. The projects Norfolk Southern is planning and doing in the region are great examples of how their long-term strategy to invest in infrastructure, operate safely and efficiently, and market their service, is designed to promote growth."
SOURCE: Norfolk Southern |
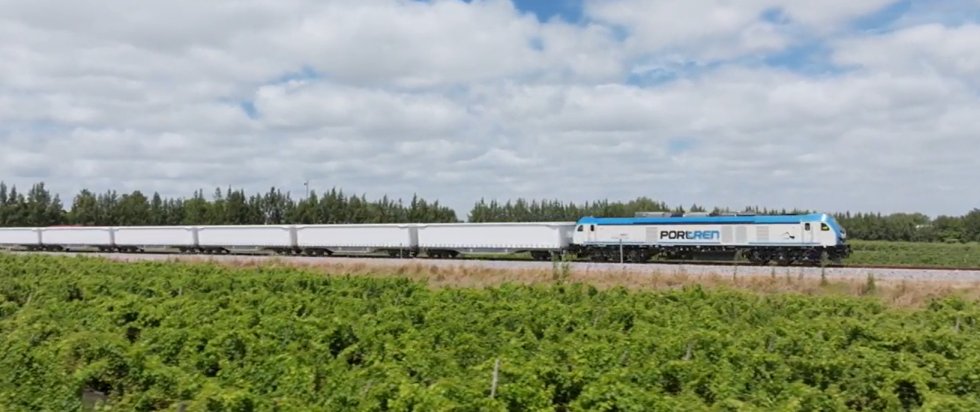
UPM’s First Pulp Transport by Rail Ran Successfully in Uruguay
April 8, 2024 – UPM announced that its first pulp transport by rail ran successfully in Uruguay last week when a train consisting of a locomotive and 14 wagons travelled from the Paso de los Toros pulp mill to UPM’s port terminal in Montevideo. This was also the maiden voyage of the Ferrocarril Central, Central Railway project of the Uruguayan Ministry of Transport and Public Works.
The reconstruction of the Central Railway line from Uruguay inland to the capital Montevideo is one of the most important infrastructure projects in Uruguay's history, carried out as a public-private partnership.
Construction work on the project, which covers a total of 273 km of track, started in 2019 and ended in 2023. After installations, testing and certification, the project progressed to commissioning, and now UPM’s pulp transports are starting to gradually move from trucks to rail.
With its cargo accounting for about half of the total freight to be transported via the rail, UPM is one of the main users of the line but the line offers new business opportunities for all Uruguayan inland industries and the possibility to develop passenger transport.
The trains are operated by DBCC Transport which is a consortium of three companies, Deutsche Bahn of Germany, Cointer Concesiones of Spain and Christophersen of Uruguay.
Paso de los Toros Pulp Mill
UPM’s Paso de los Toros pulp mill began operations in Paso de los Toros, Uruguay in 2023. The mill has the capacity to produce 2.1 million tonnes per year of eucalyptus pulp.
SOURCE: UPM |
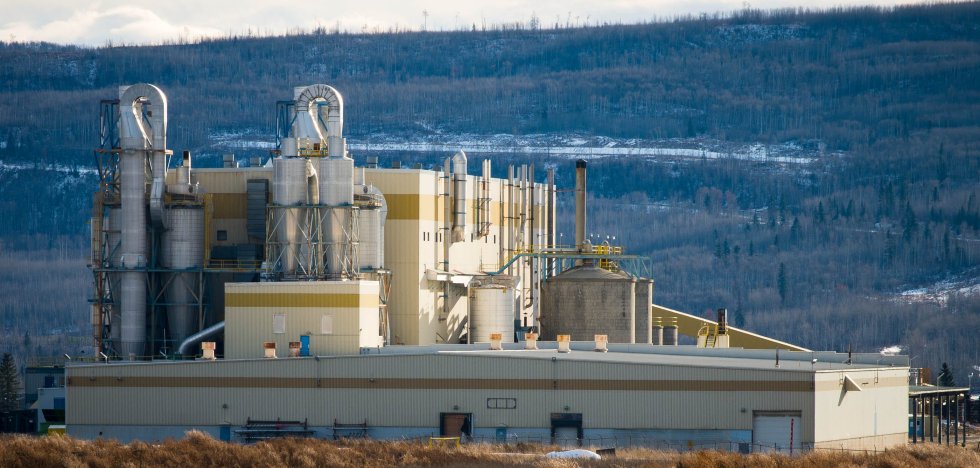
Buffalo Rail & Infrastructure has Acquired Taylor Pulp Assets from Canfor for $7 Million
March 22, 2024 - Buffalo Rail & Infrastructure Corp. ("Buffalo") on March 19 announced its $7 million acquisition of Canfor Pulp Products' recently discontinued pulp mill assets, including 300+ acres of heavy industrial land, in Taylor, British Columbia, Canada.
The Taylor pulp mill has been idle since the first quarter of 2022 due to ongoing uncertainty with regards to the availability of economically viable fibre in the region and market weakness for its product — Bleached ChemiThermo Mechanical Pulp (BCTMP). The mill has the installed capacity to produce 230,000 air-dried metric tonnes per year of BCTMP.
According to Buffalo, the property will be repurposed over time into a multi-use industrial distribution and logistics hub focused on serving the region's energy, agricultural and forestry industries.
"When one door closes, another one opens for this site," said Jarrett Zielinski, President & CEO of Buffalo. "We, along with our stakeholders at Buffalo Rail, were able to establish new uses for the discontinued pulp mill that will optimize the site's characteristics and support industrial growth in the region.
"The multi-phased, multi-year development provides a much-needed response to the changing logistics and supply chains needs of industrial participants across multiple industries and sectors in Western Canada and beyond," Zielinski explained.
Involving an estimated $50+ million capital investment in the area, the first phase of development is anticipated to see 100 construction jobs and 30 full-time permanent jobs on the site. Phase 1 is expected to become operational around Q2 of 2025.
Robert Reimer, Chief Financial Officer of Buffalo, commented, "We appreciated working with Kevin Edgson and the folks at Canfor Pulp Products Inc. on this transaction and look forward to working with the community to develop this strategically important site. The features of this site provide boundless opportunity to support the industrial growth forecast for the region."
Headquartered in Calgary, Alberta, Buffalo Rail & Infrastructure Corp. was created in 2023 by a diverse team of logistics industry veterans to capitalize on global shifts in supply chain strategy. With its mission to develop modernized rail and rail adjacent infrastructure, Buffalo is set to better service the evolving needs of North American producers and shippers.
SOURCE: Buffalo Rail & Infrastructure Corp. |
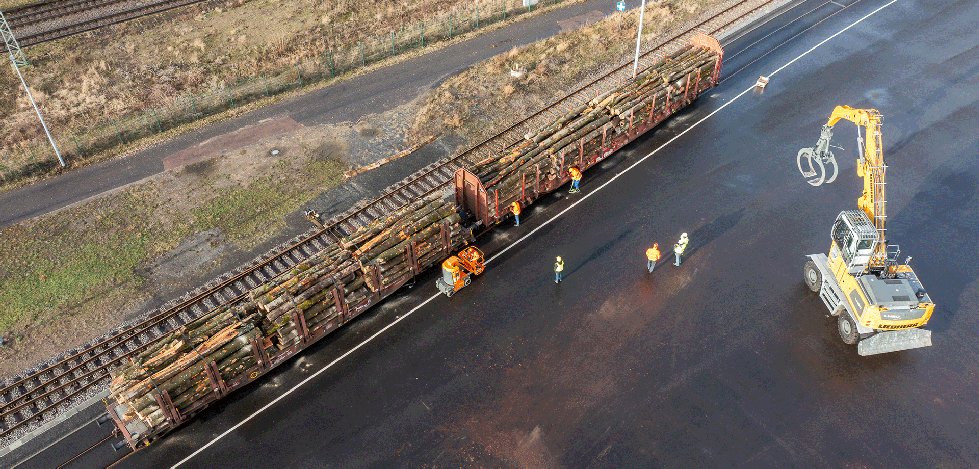
DB Cargo Makes First Deliveries of Wood to UPM Leuna Biorefinery in Germany
March 15, 2024 - UPM Biochemicals announced another important milestone in the development of the world’s first biorefinery in Leuna, Germany. In partnership with DB Cargo, the first deliveries of wood have now been made to Leuna by rail, establishing and testing the direct rail link to the Leuna operations’ woodyard. This will enable UPM to transport wood sustainably and to strengthen local supply chains, increasing the security of supply with critical raw materials. DB Cargo, specialists in the sustainable and climate-friendlier transport of goods, is a long-standing partner for timber transportation in the rail sector and has been handling UPM’s paper and pulp freight for several years.
“We are excited to welcome the first rail-based wood transports at our newly established wood yard in Leuna,” said Andreas Meggendorfer, Director Supply Chain & Sourcing at UPM Biochemicals. “We will offer fully sustainable renewable chemicals with a significantly better CO2 footprint compared to fossil alternatives. It is paramount that we work on strategies to continuously optimize the environmental performance of our products further. Using rail as a transport mode does exactly that. And by partnering with DB Cargo, we can now rely on a well-known and capable rail logistics partner and have built a resilient and sustainable wood logistics setup for our biorefinery in Leuna.”
“UPM and DB Cargo have been linked by a successful partnership for rail-based inbound logistics of timber for many years. We are therefore very pleased to now be an important supply chain partner for UPM at the new biorefinery in Leuna,” said Thorsten Wartenpfuhl, SVP Sales Consumer Goods, Pulp & Paper, Timber at DB Cargo.
It is worth mentioning, that wood handling and processing activities have started as part of the commissioning and start-up work for the biorefinery. The first wood chips made of wood from sustainably managed regional forests have been produced, confirming the overall progress made on-site.
UPM is investing EUR 1,180 million to build the world’s first industrial scale biorefinery in Leuna that will convert sustainably sourced, certified hardwood into next generation biochemicals – enabling the vital shift away from fossil-based to renewable materials across a wide range of industries. The Leuna biorefinery is part of a broader growth area, UPM Biorefining, that is scaling refineries to produce a variety of renewable fuels and chemicals made from sustainable biomass.
SOURCE: UPM |
|
|